
Types of Loading Docks
Last updated on 11/16/2022Whether you’re opening your own warehouse or looking to improve your distribution process, being able to identify the different types of loading docks is essential. Choosing the wrong dock can limit your staff’s efficiency and cause disruptions in the shipping and receiving process. In this article, we’ll investigate what a loading dock is, the different types of docks you can choose from, and what sets them apart.
What Is a Loading Dock?
A loading dock, sometimes referred to as a loading bay, is an area in a warehouse, manufacturing plant, or distribution center where goods are loaded and unloaded. Loading docks ease the burden on carriers and provide a convenient space for moving goods. They are a key part of a business’s infrastructure and play a significant role in the transportation of products.
Loading Dock Parts
Loading docks are complex areas that require several different types of equipment to function effectively. For that reason, it’s best to familiarize yourself with each component. Below, we’ve listed some of the most common loading dock parts and what they are used for:
Shop All Loading Dock Equipment- Access points: When a vehicle arrives, the driver is required to enter your facility and drop off paperwork. An access point provides them with a convenient way in and out.
- Bumpers: Bumpers are designed to protect the structure of your building and prevent vehicle damage. They create a buffer between vehicle and wall, ensuring against costly collisions.
- Leveler: A dock leveler helps maintain the height difference between a loading dock and a trailer. It allows forklifts and other types of warehouse equipment to maneuver with ease and protects against trips, falls, and other accidents.
- Lift: The dock lift improves accessibility. It serves a similar function as a dock leveler, helping to bridge the gap between dock and truck.
- Lights: Dock lights keep your workplace lit, reducing the risk of damage and ensuring an optimum working environment.
- Overhead door: Overhead doors offer additional protection from the elements and are designed to keep up with a fast-paced work environment. They keep goods and equipment safe and must be maintained regularly to ensure efficiency.
- Restraints: Restraints keep a vehicle from moving while it is attached to your loading dock.
- Shelters and seals: Shelters and seals create an air-tight barrier around the back of a vehicle when it arrives. They keep rain, snow, and extreme temperatures from affecting your loading dock, maintaining a climate-controlled environment.
Warehouse Loading Docks
In general, there are five different types of warehouse loading docks. Though every dock is intended to serve the same purpose, each variation functions differently from the next. Each type of dock also comes with its own set of advantages and disadvantages. For that reason, you should choose the type of loading dock that best fits your warehouse concept. The different types of loading docks are as follows:
1. Flush Dock
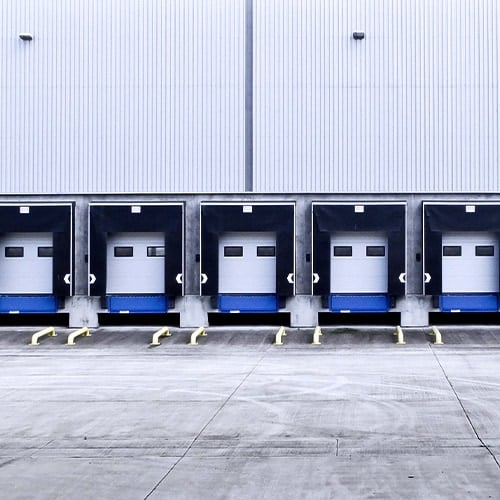
A flush dock, sometimes referred to as a standard dock, is one of the most popular types of loading docks. These docks are designed to fit perfectly within your loading zone. They feature large, individual entryways and allow trucks to seamlessly attach for loading. In many cases, flush docks are designed with shock-absorbing bumpers to prevent structural damage to the facility.
Since flush docks do not protrude from your building, they allow you to make the most of your warehouse space. Flush docks are typically used in commercial shipping and are a convenient option for transporting large objects. They are also the most popular choice for small businesses. It’s important to note that since flush docks are built into your facility, you’ll be able to store goods inside and keep them protected from the elements.
Back to Top
2. Enclosed Dock
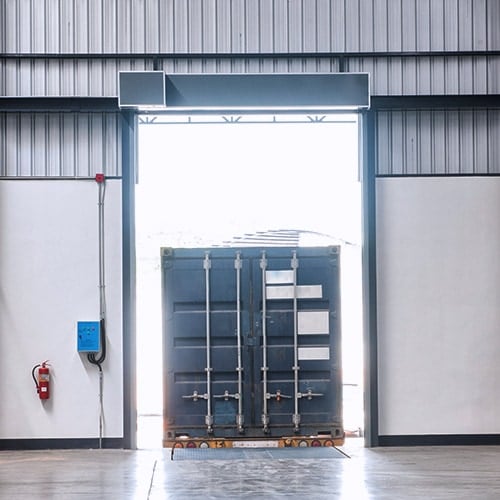
An enclosed loading dock allows an entire vehicle to park in a garage-like environment. Since they are indoors, enclosed docks offer complete protection from the elements and are ideal for handling temperature-sensitive goods. They also allow for increased security compared to other docks. Though they are relatively rare in the warehousing industry, enclosed docks are typically used by companies overseeing large fleets of trucks.
Though enclosed loading docks offer advanced security and weather protection, there are several considerations one must take into account when building their own. These include:
- Space: Be sure that you have enough space for vehicles to park and maneuver. An enclosed dock should also have enough space for forklifts and other necessary equipment to move without obstructions.
- Ventilation: Any vehicle or motorized equipment in your enclosed dock will give off exhaust. Because of this, you must have a functional ventilation system in place to keep you and your employees safe.
- Layout: Be sure that your enclosed dock space is simple and organized. Since multiple vehicles may be parked at a time, a simple layout makes it easier for employees to find what they’re looking for.
Back to Top
3. Sawtooth Loading Dock
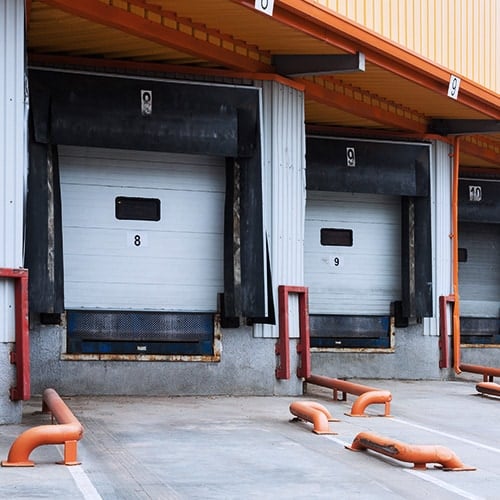
A sawtooth loading dock consists of several smaller docks, with each dock positioned at an angle. This helps to save space outside of your facility, allowing you to load more vehicles at a time. These docks also allow you to simplify your roadway and yard approaches, allowing vehicles to navigate tight or narrow spaces with ease. Sawtooth docks are typically used in large-scale manufacturing operations or by warehouses with ample storage space.
While sawtooth loading docks can save space outside, their angled layout limits the indoor space of your facility. Without proper planning, this can restrict your staff's room to work, decreasing productivity. For that reason, you must be mindful of the space available to you to ensure a convenient loading dock layout.
Back to Top
4. Depressed Loading Dock
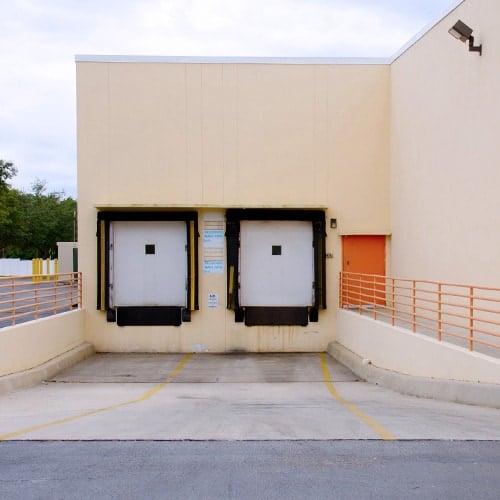
A depressed loading dock, sometimes referred to as a declining loading dock, functions similarly to a flush dock. The key difference between the two is that a depressed dock features a sloped driveway. Depressed docks are often used by facilities with basement loading areas or separate dock levels. When using a depressed loading dock, vehicles are instructed to back in at an angle determined by the decline of the driveway.
When designing a depressed loading dock, there are multiple factors to take into account. These include:
- Decline angle: The angle of your driveway should not exceed 10%. Failure to do this can increase the risk of accidents.
- Weather conditions: Snow, rain, and other hazards can make it difficult for trucks to operate, as they can experience traction problems on a decline.
- Vehicle damage: Be sure to design a loading area that minimized the risk of damage while vehicles maneuver your dock.
Back to Top
5. Open Dock
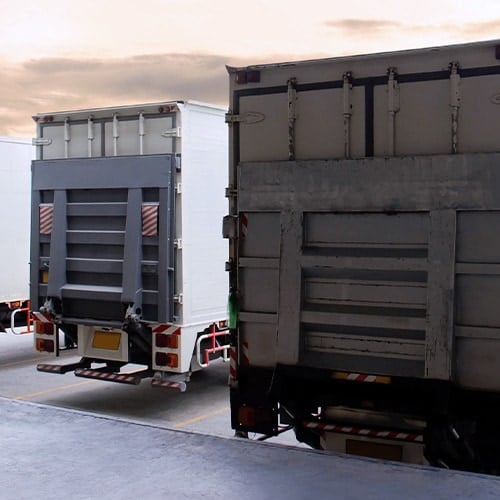
Open loading docks consist of an outdoor platform with space to store goods. In most cases these platforms feature an overhead canopy, leaving the rest of the dock exposed. It's important to note that of the five different types of loading docks, open docks are the least recommended. This is due to a variety of different factors that can impact safety and working conditions. Because of this, open docks have grown increasingly rare and are typically only used under certain circumstances.
Open Loading Dock Pros and Cons
Though open loading docks aren’t popular, they do come with certain advantages. The two main advantages associated with open loading docks are as follows:
- Flexibility: The lack of walls or barriers of any kind provides easy access for your staff and allows them the flexibility to work as they see fit, saving valuable time in the workplace.
- Organization: Their open design also gives you the freedom to organize and reorganize your dock as needed.
Despite their advantages, open loading docks are prone to several weaknesses, which is why they aren't recommended in the industry. Some key disadvantages associated with open loading docks include:
- Vandalism: Because of their design, open loading docks are prone to theft and provide minimal security.
- Lack of temperature control: Open loading docks cannot be heated or cooled efficiently, posing a risk to temperature-sensitive products and resulting in uncomfortable working conditions for your employees.
- Lack of protection from the elements: Many open loading docks are vulnerable to flooding, freezing, strong winds, and other hazards. This can create an unsafe working environment, damage your goods, and impact productivity in the workplace.
Back to Top
Loading Dock Design
Although loading docks can vary significantly in style, each dock must be designed with certain factors in mind. These factors can dictate your loading dock’s layout and can disrupt your business if ignored. As you design your loading dock, keep the following aspects in mind:
- Roadway approach: Roadway approach is the path vehicles take as they enter or exit your facility from the main road. Design your roadway approach so that vehicles can drive in rather than have to back in.
- Yard approach: Yard approach is the path vehicles take to enter your loading dock once they’ve turned off the road and into your facility. Since it’s easiest for truck drivers to make left-hand turns, plan your yard approach to allow for counter-clockwise traffic.
- Apron space: Apron space is the area between your loading platform and the nearest obstruction. It should be planned around trailer movement to ensure each vehicle has enough space to maneuver.
- Landing strip: In high heat, truck landing gears can sink into asphalt when lowered. This can result in damage to the vehicle and decrease productivity. To prevent this, a concrete landing strip should be positioned at each dock to reinforce your parking area.
- Waiting area: If your loading dock is busy, some vehicles may need to wait their turn to dock. To prevent confusion and ease traffic, provide them with a waiting area.
Back to Top
Loading docks are an essential part of the distribution process. They can be found in most warehouses or distribution centers and come in five distinct forms. By adhering to the information above, you’ll be able to make an educated decision on which type of loading dock best fits your needs.