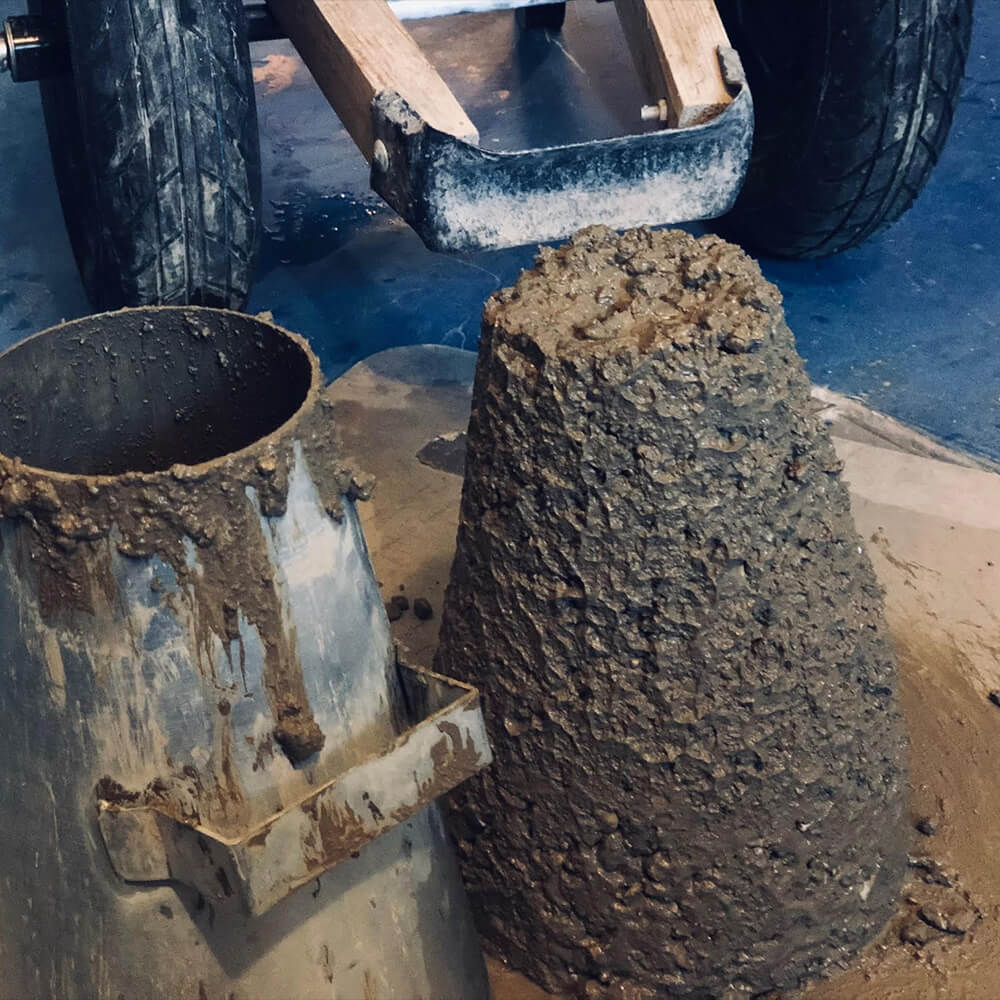
There is a public disagreement in the concrete and construction industry regarding the concrete slump test. But who specifically disagrees and why?
Let’s take a few minutes to break down both sides of the concrete slump test controversy and how it can impact a project.
What are the reasons for the concrete slump test controversy?
There are three distinct causes that result in this controversy. Let’s break down what these causes are, how they occur, and what they can impact.
Ordering the incorrect slump when ordering the concrete
Oftentimes what we see on a concrete job site is that a contractor will order a slump that is lower than what they actually need.
For example, a concrete contractor would want a 6 to 8 inch slump; however, they’ll order somewhere between a four to a seven inch slump from the provider.
As it turns out with transit (especially during the warmer times of the construction season), the concrete slump will be reduced due to one of the following reasons:
- Ambient temperature
- Batch temp
- Haul time
- Concrete Admixtures (like Accelerators and Crack Compensators)
At this point, the contractor and the Ready Mix truck driver must add water or a water reducer to get to the slump that is actually needed on the jobsite.
Misuse and incorrect testing procedures when employing the slump test
This is probably the biggest aspect of the slump test controversy. The concrete slump test is an unforgiving test. Two components buried within the standard operating procedures include:
- The instructions on what speed to pull the concrete slump cone
- The need to be cognizant of no lateral deformation during the twisting or pulling of the cone
The concrete slump test is difficult to do right even in the perfect conditions of the laboratory. Because of this, the concrete slump test becomes ever less forgiving when added to the complexities of the job site and the changing conditions of the ambient environment.
Slump testing requires skilled labor (or even better stated, an artisan), and as it turns out, there has been a major exodus of skilled labor in the concrete technician industry.
Misinterpretation of the slump data
Misinterpretation of the slump data is often easily overcome through education. At one time, the water/cement ratio slump, the slump, and the strength could all be tied together. However, with the advent of noon emerging water reducers over the last 30 years, slump and workability cannot be directly related to water/cement ratio and strength.
The slump test for concrete is a quality control test that is used or can be used by the purchaser to determine if the material that they bought is the material that they purchased. What does this mean? The slant of the swamp concrete that is received and measured on the job site should have a uniformity (or a similar slump) to what was ordered from the concrete provider and what is on the batch ticket. Slump can also be used to and for the workability and placeability of the concrete mixtures for specific job sites.
Who does the slump controversy impact?
The slump test controversy impacts the concrete provider, purchaser, concrete owner, and concrete contractor.
Whether it is rejected trucks due to incorrectly measured slumps or an incorrect addition of water (to adjust the slump to design values after transportation to the field), the incorrect slump values can cause unpredicted concrete costs on a construction jobsite.
These costs can include but are not limited to:
- Concrete waste from ordering new concrete patches
- Delay in the construction schedule
- The need for more raw materials
- The incurred cost on the environment
What does all of this mean for the industry?
There’s a lot involved with the potential drawbacks of the concrete slump test. But the question is: where do we go from here?
Do we continue to deal with faulty data and the consequences that stem from that faulty data? Or do we demand more of our industry and provide further continued education and support? Or… do we find another way?
Is there an alternative out there that we have yet to uncover or do we simply need to build better, more detailed standards and demand more accountability of our civil engineers on the jobsite?
Let us know what you think.
Buenas tardes,
La verdad con mucho respeto debo decir que para esta prueba no se requiere de un “experto” simplemente se necesita tener claro el método y con esto ya la prueba debería salir sin ningún problema.
Este ensayo es la mejor forma de identificar esa calidad de entrega de hormigón, por tanto no creo razonable siquiera pensar en dejar de lado esta prueba tan importante y que definitivamente nos brinda una buena idea de lo que estamos a punto de recibir en la obra.
Ahora los profesionales que se encargan de pedir el producto, si deben tener claro que necesitan y entender que las plantas de hormigón están en plena capacidad de entregar un buen producto, somos nosotros en obra quienes debemos actualizarnos y tomar decisiones técnicas y apoyadas en el mismo desempeño del producto y buenos elementos. Una saludo
There are a few issues here.
1) Specifications may be cut and paste from project to project by the civil engineers to keep costs down but needs to be uniquely assessed and job specific. For example:In a block of flats suspended floors might be specified at 32MPS, 20 agg, 80 ml slump or 32/20/80. Let’s say this concrete is being pumped 20 metres horizontally through steel pipes then goes through a 90 degree angle to be pumped vertically through steel pipes to reach the suspended floor. Then it goes through another 90 degree angle followed by steel pipes for 10 metres followed by a reducer into 20 metres of flexible rubber pipe which then discharges the concrete in to the slab. The question is, is 20/32/80 an appropriate design. The answer is no, but that is what the civil engineers requested at tender stage based on cut and paste specifications. The whole design is now flawed. This is why on unsupervised building sites there is the constant high revolution whirr of the concrete agi drum because water has been added to make it pump but this weakens the concrete leading to potential compressive strength failure. The specification should read for this scenario 32/20/150 or 32/20/180, as this is how the concrete is being placed.
2) The industry itself has no mandated minimum requirements for concrete technical management roles in Australia. In the UK the industry requires people to have 5 years minimum technical experience plus concrete technology qualifications. Here in Australia, you don’t need any role specific qualifications or time in a supervisory role. You could have a degree in ceramics or home economics or another totally irrelevant subject and still get the job title of technical manager responsible for mix design, and all other aspects of concrete quality.
3) Here in Australia builders can self certify their own quality of the build so don’t need to pay for any testing and can add water to an unsupervised site agi to help with placement. There needs to be an independent observer/certifier I.e. an old fashioned clerk of works to certify all aspects of the build such as construction drawings replicated by placement of steel, concrete, layout etc. this is not happening on all sites because it is not a mandated requirement in Australia.