In an exclusive chat, Dhirubhai Shah, Chairman, Shahlon Silk Industries Limited, spoke about the company’s history, its product offerings, manufacturing infrastructure, impact of the pandemic on the business and future plans. Here are the excerpts
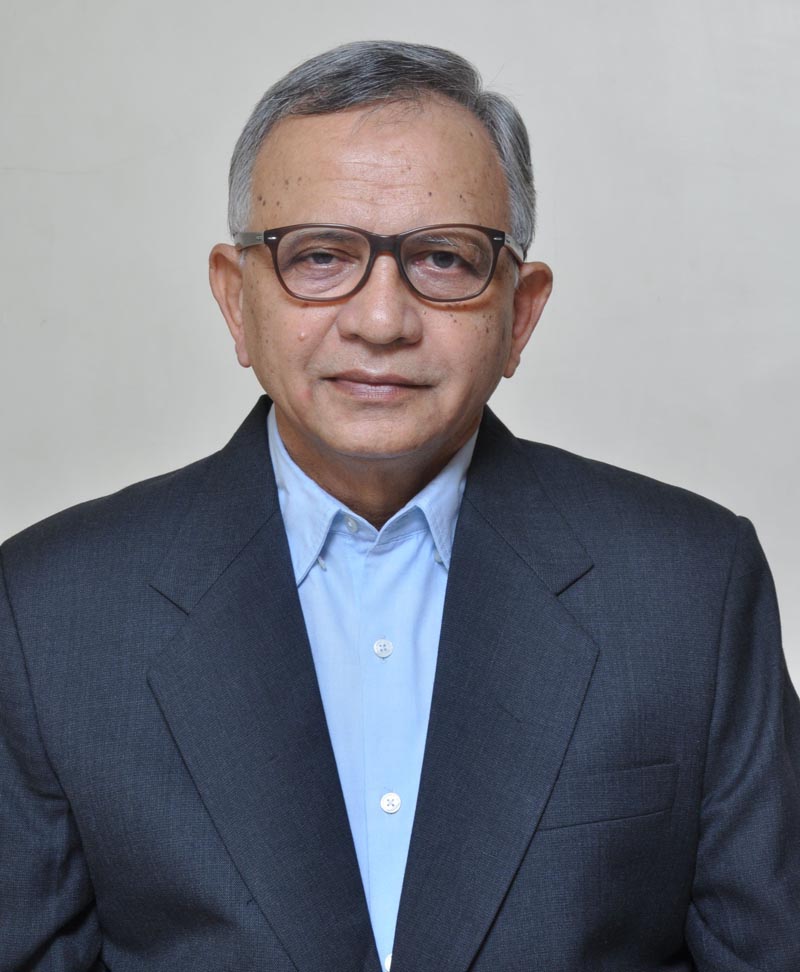
Shahlon Silk Industries Limited (SSIL), a leading fashion to technical fabric player catering to leading domestic and international fashion brands across the world, has its base in Surat, a key textile hub of the country. With the unwavering vision to be a fully integrated textile enterprise that finds strong support from its workforce of more than 1,800 employees, the company has expanded from being a yarn marketing agency to texturizing, twisting, sizing, yarn dyeing, weaving, finish fabrics and industrial infrastructure fabric player in India.
Established in 1984, SSIL is engaged in manufacturing and exporting supreme quality fabrics and synthetic textile yarn across the world. It has three state-of-the-art manufacturing units in Gujarat located at Kim, Karanj and Kosamba. Founded by brothers Dhirubhai Shah, Arvind Shah and Nitin Shah with vast experience in the textiles business, three second-generation children joined the family business in 1990, 1995 and 2015 respectively. Providing an overview of the company’s product portfolio, Dhirubhai Shah says, “With four manufacturing units situated in Gujarat, the company is a fully integrated textile enterprise primarily engaged in the manufacture of all types of fabrics and yarns.”
“SSIL’s products cater to the weaving and garment industry. The company provides all its customers with a completely new level of yarn and fabric sourcing. With an inventory system that comprises a wide range of yarns and fabrics to choose from, we offer a one-stop solution for all fancy yarn and fabric needs,” he adds. The total installed capacity of its three plants for manufacturing fabric is 40 million metres per annum and 21,000 tons per annum for yarn. In the yarn segment, the company produces polyester yarn from 30-300 denier with a presence across all types of textured yarn, carpet yarn, dyed yarn and sized yarn.
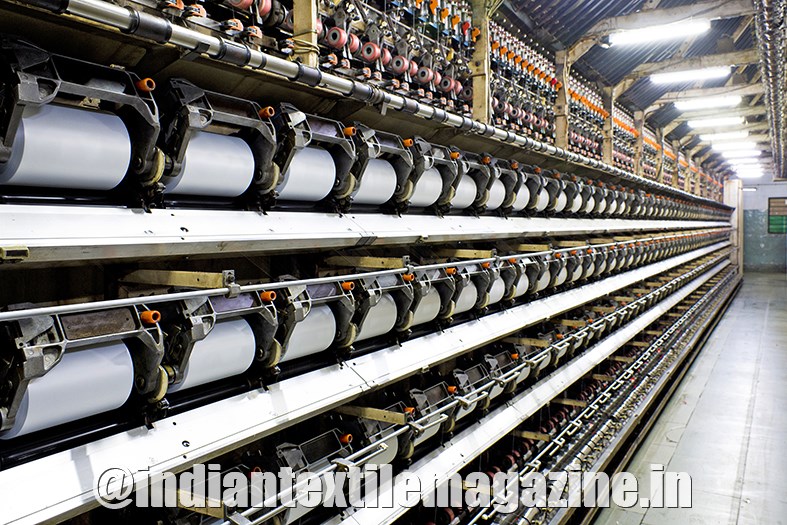
In the fabrics segment, the company has an established presence across different types of fabrics like solid dyed, jacquard and yarn-dyed, printed, sustainable and greige for fashion and furnishings products. “The company went public in 1994 and raised about Rs 3 crore. In the initial phase of our business during 1984-2000, it operated with just 12 conventional power looms and 282 water-jet looms,” Shah informs.
“We have been a marketing agent of Reliance Industries and our association with them for synthetic yarn during the period has been one of the key milestones,” he adds while elaborating about the key achievements of SSIL since its establishment. “During 2001-10, the company expanded its production capacity with installation of 100 water-jet looms and incorporated wind energy for the production processes. Post 2011, it has seen tremendous growth with commencement of yarn dyeing and has further expanded its capacities,” Shah says.
International Presence
Throwing light on the company’s key export markets, Shah informs: “SSIL exports fabric to Sri Lanka, South East Asia, Myanmar, Cambodia and USA. With presence across 15 countries, exports contribute about 14% to our revenues. However, due to the external constraints and supply chain disturbances on account of ongoing pandemic, we have not received any export order. We expect normal operations to resume before the year-end when the situation across major markets is expected to improve. We are ready for global challenges as our product portfolio is competitive enough for supply to Turkey, Israel, Morocco, Thailand and other yarn consuming countries where SSIL has made its presence felt in recent years.”
When asked to name some of the important global brands that the company supplies to, Shah informs: “There has been a demand growth for fabrics and yarns over the years led by increasing demand for fashion and furnishing products. The company is a leading player in fabric used in women’s wear like sarees and garments. These are growing segments. In fact, they have been posting growth in double digits. Shahlon Silk Industries supplies synthetic fabrics to top international brands like M & S, Matalan, Ann Taylor, Belk, and many more.”
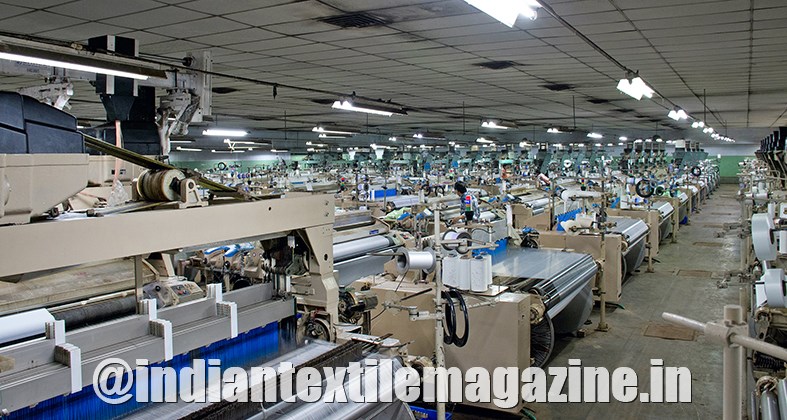
Focus on Quality
Given that there are thousands of similar yarn and fabric manufacturers vying for limited market share, what is it that makes SSIL different? Surely then there must be advantages that the company offers in terms of product quality, service, innovative offerings? Responding to this query, Shah says, “At SSIL we continuously invest in state-of-the-art technology and equipment across all our areas of operations to adopt globally accepted manufacturing technology – delivering speed, versatility and most importantly, quality.”
“In fact, product quality is of supreme importance for us and we ensure exceptional quality control across our entire manufacturing process through extensive testing methods to adhere to all quality specifications,” he adds. Sharing details about how the company has been able to tide over the impact created by the corona virus pandemic, Shah elaborates, “The offices were shut down during lockdown phase but the company adopted the work from home policy for office-related work during the entire duration. With the partial easing of the lockdown restrictions, the company has restarted its operations at all its manufacturing plants and at the Surat office in a gradual manner from April 27, 2020.”
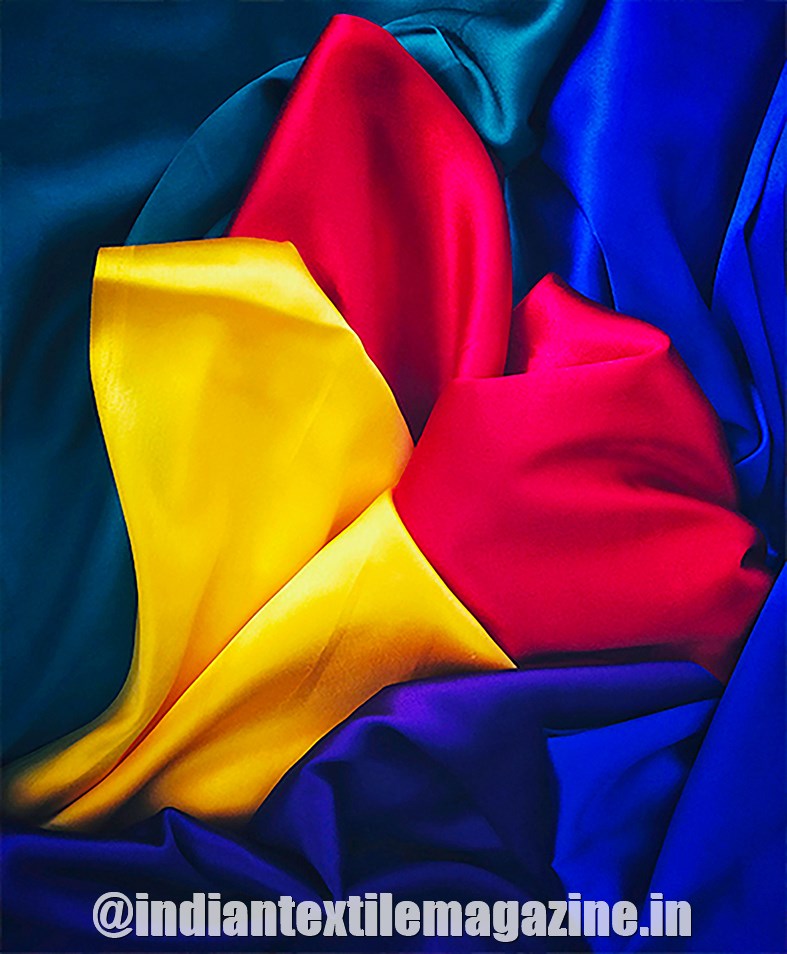
“At all the locations, necessary arrangements of sanitization, self-quarantine and screening, etc. have been made and are continuing. Though the overall capacity utilisations of our plants have been impacted in the last two months due to constraints and supply chain disturbances, we are confident of getting back to the normal levels in this quarter. The company is putting all its efforts to convert this challenge into opportunity by rationalising the manpower cost and downsizing the other cost centres, while also making efforts to retain and add more customers for sustaining and increasing the demand,” he adds.
Financial Status The company has been clocking impressive growth rate over the years. Speaking about the company’s current turnover and annual growth over the last few years, Shah reveals, “The company’s turnover for FY20 stood at Rs 382 crore. For the year ended March 2019, although revenue was marginally up from Rs 529 crore to Rs 532 crore, net profit after tax was up by 40 per cent from Rs 2.64 crore to Rs 3.72 crore. The share trades at Rs 37, accounting for a market capitalisation of Rs 68 crore.”