Rethinking the Kaplan turbine
The StreamDiver takes off in the USA
EREF successfully lobbied for hydropower
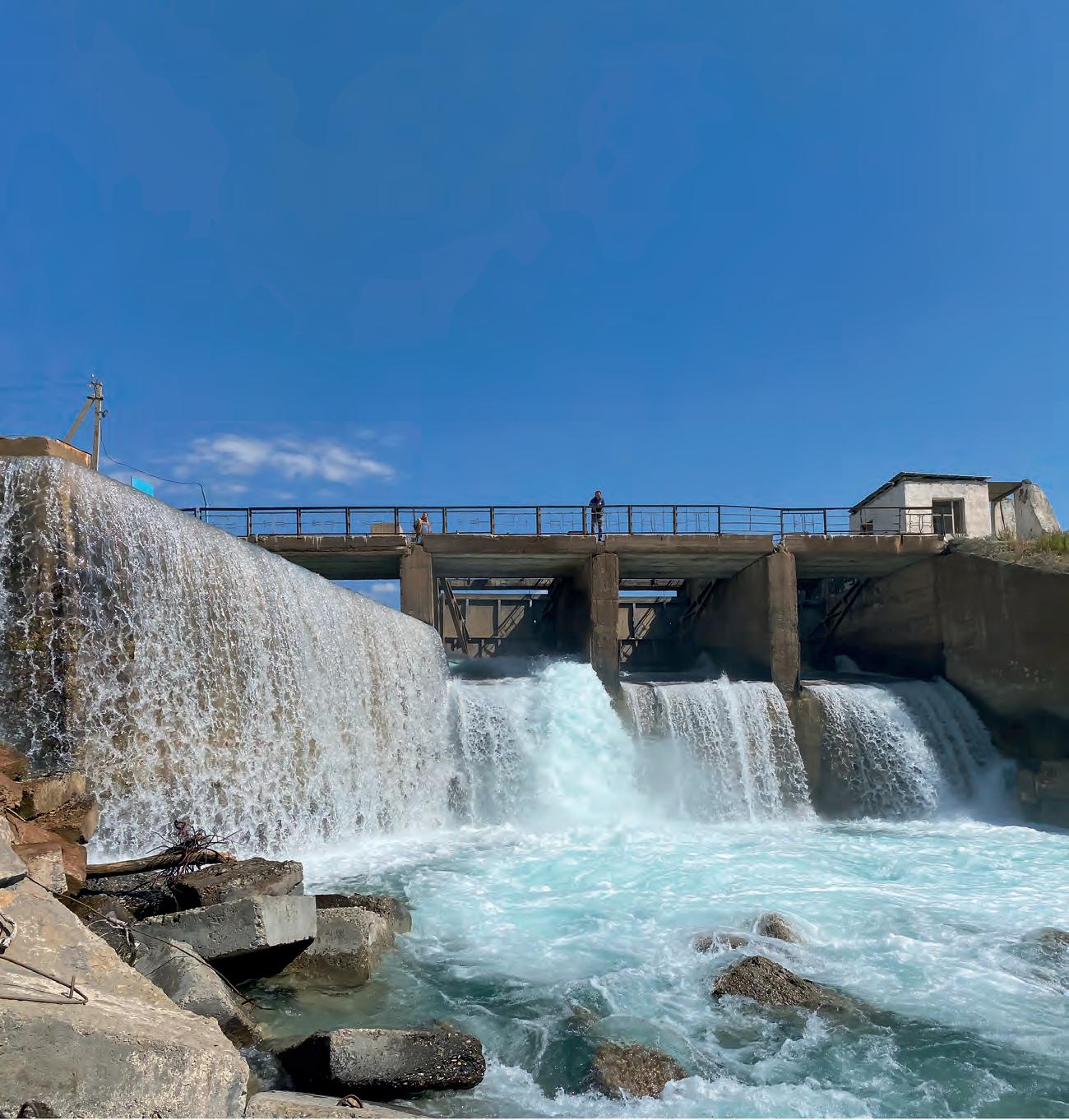
Dak Di1 hydropower plant in Vietnam is online
Weir equipped with Switzerland’s widest Coanda
Rethinking the Kaplan turbine
The StreamDiver takes off in the USA
EREF successfully lobbied for hydropower
Dak Di1 hydropower plant in Vietnam is online
Weir equipped with Switzerland’s widest Coanda
GLOBAL Hydro combines innovation, digitalization, and long-term thinking to create sustainable hydropower solutions for future generations. We turn your vision into reality and support you throughout the entire life cycle of your power plant – around the world.
Energy has long since become a widely-debated issue in society at large, not least due to our unfortunate dependence on Russian gas. The political context has boosted general approval for the expansion of renewable energies. Indeed, there has never been more support for this changeover than today. People are realising that expanding the use of renewables can reduce the dependence on gas, counteract the climate crisis and keep prices down. Similarly, it has become clear that a transition to an economy driven by renewable energy resources may be achievable earlier than previously assumed – as was strongly affirmed by the latest edition of the annual International Energy Agency (IEA) publication – the Electricity Market Report. According to the study, a mix of renewables and nuclear power, the resurgence of which has been officially approved in many places, will account for more than 90% of global growth in the demand for electricity in the next three years. On a positive note, this will increasingly push fossil-fuel-based energy sources out of the market, and IEA scientists believe this will lead to the highly desirable effect of CO2 emissions from global electricity generation hitting a plateau, or even falling away. The less good news is that, in general, for the period between 2022 and 2025, the authors of the study forecast an increase in global electricity demand of around 2,500TWh to almost 29,300TWh – a remarkable growth of around 9%. Expressed another way, in total this growth alone roughly corresponds to the entire electricity consumption of the European Union. Five letters explain the steep demand curve rise: C-H-I-N-A. By 2025, this immense nation will account for one third of the world‘s electricity demand. In comparison, in 1990 China’s electricity consumption made up 5% of the global total. When added to extraordinary growth in demand in other heavily industrialised regions on the Asian continent, by 2025 Asia will consume more than half of the world’s electricity. Although an increase in the demand for electricity is also expected in North America and Europe, statistically – compared to these booming Asian nations, the share of the growth in demand accounted for by the ‘old’ industrial giants is declining. There is, however, a silver lining! The bottom line of the new Electricity Market Report is a positive one: The triumphal march of the renewable energies has finally begun! Globally, by 2025, these energy sources will amount to a capacity of 10.8TWh, for the first time overtaking the capacity provided for by environmentally-unfriendly coal-powered electricity production.
Contrary to numerous prophecies of doom, belief in the fact that hydropower has a central role to play in the global expansion of the use of renewables is growing in line with these developments. Recently, Chinese scientists published a new study in a specialist journal: Nature Water. According to the study, global hydropower capacities could be doubled to 9 petawatt hours, so hydropower could play a key role in the fight against climate change. It’s no surprise the greatest potential (around 85%) is still unused – in Asia and Africa – so these are the greatest sources of hydro-powered hope for the future. It can be safely assumed that the European hydropower industry, with its leadership in know-how, can – and will – play a major role in driving this expansion.
I wish all our valued readers an enjoyable and informative time reading the latest edition of zek HYDRO.
Best regards,
Roland Gruber Editor-in-Chief13
[ VIETNAM ]
16 Makari Gad hydropower project achieves outstanding feat [ NEPAL ]
18 New hydropower station as part of a wide-ranging synergy project [ ITALY ]
21 Power plant generates clean electricity for 200,000 households [ GERMANY ]
24
[ POLITICS ]
26 Renown US-university chooses Voith Hydro’s StreamDiver [ USA ]
28 Hydro-Construct built largest rubber dam of India [ INDIA ]
31 Small-scale hydropower station develops Styrian water body [ AUSTRIA ]
34 Viennahydro in tune with the international hydropower developments [ CONVENTION ]
36 Ski resort achieves partial energy autarchy with hydropower station [ ANDORRA ]
38 New suspended solids concentration (SSC) measurement [ TECHNOLOGY ]
41 Weir equipped with Switzerland’s widest Coanda system to-date [ SWITZERLAND ]
44 Kaplan EVO – rethinking the Kaplan turbine [ TECHNOLOGY ]
48 Ecological upgrade and enhanced performance at Grépiac power plant [ FRANCE ]
50 No valve is too big for these industrial specialists [ TECHNOLOGY ]
53 High operational availability with customised generator technology [ TECHNOLOGY ]
56 Bavarian supplier of complex formwork for hydropower projects [ TECHNOLOGY ]
58 New PELFA management trio shows its steel on the hydro market [ INDUSTRY ]
60 A potentially deadly problem gains attention due to climate change [ ECOLOGY ]
62 Watertight AUMA actuators for underwater hydro turbine control [ TECHNOLOGY ]
In October '22, commissioning of the new machine 1 marked the completion of one of the most important revitalisation projects in Austrian hydropower history. Over the past eight years, all six turbines and generators dating from the 1950s at the Ybbs-Persenbeug power plant, the oldest of its kind on the Danube, have been replaced with modern, highly efficient machine sets. VERBUND has invested one hundred million euros in the Danube power plant project. Annually, the new infrastructure is expected to deliver around 1.4 billion kilowatt hours of renewable electricity from hydropower to the Austrian grid. Conversion will improve reliability and raise the volume of power generated by more than 77 million kilowatt hours to a total of 1.4 billion kWh. The resulting 6% increase in efficiency corresponds with the annual electricity consumption of 22,000 households, and an annual CO2-emissions saving of 62,000 metric tons. All this was achieved without the need for structural intervention in the surrounding area. “This successfully-implemented renewal project is a prime example of how we are fighting the climate crisis,” states Achim Kaspar, member of the VERBUND management board with responsibilities for generation, digitalisation and sustainability.
Voith Hydro officially opened the doors of its newly established center of competence for generator components in Bosnia and Hercegovina a few months ago. The location in Lukavac will be serving western markets; from North and Latin America to Europe and Africa. The new location is only 1.5 flight hours away from Voith Hydro’s German headquarters in Heidenheim. Its’ set-up was closely aligned with experts from the company’s central technology department in Germany, where essential R&D functions for generator components are based. Apart from the proximity to the headquarters, customers benefit from the closeness to the mainly European supplier base of insulation materials which ensures efficiency and smooth operations. Additionally, Voith Hydro is in close collaboration with the Bosnian facility of ELIN Motoren, a Voith company, which is successfully producing motor and generator coils as well as wind generator components in the immediate neighborhood. Works at the facility began in 2021 and initial test productions could already be performed in February 2022. The success speaks for itself: the company’s project pipelines for all production lines (poles, bars, and coils) are filled.
PUBLISHER
Mag. Roland Gruber
PUBLISHING HOUSE
Mag. Roland Gruber e.U. zek-VERLAG
Brunnenstraße 1, A-5450 Werfen
Phone: +43 (0)664 115 05 70
office@zek.at
www.zek.at
EDITOR-IN-CHIEF
Mag. Roland Gruber, rg@zek.at
Mobile +43 (0)664 115 05 70
EDITOR
Mag. Andreas Pointinger, ap@zek.at
Mobile +43 (0)664 22 82 323
CHIEF OF ADVERTISMENT
Mario Kogler, BA, mk@zek.at
Mobile +43 (0)664 240 67 74
PRODUCTION
Mag. Roland Gruber e.U. zek-VERLAG
Brunnenstraße 1, A-5450 Werfen
Phone +43 (0)664 115 05 70 office@zek.at
www.zek.at
TRANSLATION
Crossing Paths Communication
Mag. Andreas Florian andreas@crossing-paths.net
Roger Lord
Sprachdienstleistungen
www.roger-lord.at
Übersetzungsdienst Dialogticket.com
www.dialogticket.com
PRINTING
Druckerei Roser
Mayrwiesstraße 23, A-5300 Hallwang
Phone: +43 (0)662 6617 37
POST OFFICE
A-5450 Werfen
BASIC GUIDELINES
zek HYDRO is a non-partisan trade publication focussing on hydropower
PRICE INC. POSTAGE
€ 16,- / copy incl. VAT
zek HYDRO is published annually
Circulation: 4800 copies
201920025
Construction work is underway to establish the world’s highest situated power station on the Huang He river, also known as the “Yellow River,” in the country’s Qinghai province. According to recent reports in the state-run media, the project, which was begun in 2011, is now nearing the finish line, with regular operation expected to commence in early 2024. What makes this facility special is the fact that its water source at the Maerdang dam is located in the headwater region of the Huang He, more than 5,000 metres above sea level. As reported by the state-run media, this makes it the highest-located facility of its kind. Location aside, it is also extremely powerful: with its installed hydropower capacity of 2,200MW the power station is expected to provide about 7,304TWh of clean energy per year. This brand-new facility in the Qinghai region is operated by China’s state-owned power utility, China Energy. •
•
Shortly after winning the 2022 British Steel Design Awards late last year, the new hydrodynamic screw operated on the River Ness was also announced as the winner of the prestigious National Construction Award. Previously, the system had already won the Scottish Highlands & Islands Energy Award as 2022’s best onshore-renewable project. Housed in a conspicuous, stainless steel covered building, a modern hydrodynamic screw is spinning busily to make full use of the River Ness’ hydropower potential. The 92kW machine provides about 550,000kWh in a normal year, thereby achieving an annual CO2 reduction to the tune of 140,000kg. The power generated is supplied next door to the Inverness Leisure Centre, a popular sports and wellness facility, which happens to be one of the region’s major energy consumers. There are already plans to present Project Hydro Ness more fully to the city’s many visitors. Video displays and explanatory signposts are already in the works. With about 280,000 visitors a year, the northern Scottish city of Inverness ranks fourth among the UK’s most visited cities.
•
In late March Messezentrum Salzburg opened its doors to host Renexpo Interhydro for the 13th time in a row, once again serving as an international meeting point for the hydropower industry. As usual, the event offered a comprehensive, Europewide overview of current political, marketspecific and industryrelated developments in the hydropower industry. Around 1,200 visitors took the opportunity on March 30th and 31st for a live update on the latest and greatest regarding the clean energy source. The trade fair not only serves as an exhibition venue, it is also considered an indispensable hub event for the European hydropower industry. “If we want to achieve the envisioned energy turnaround, hydropower will have to play an even more prominent role. Renexpo Interhydro offers a crucial European platform for an intense exchange of ideas,” says the trade fair centre’s managing director, DI (FH) Alexander Kribus, MBA, in explaining the event’s relevance.
To further expand power generation in the canton of Valais, the government recently introduced 8 hydropower projects that being considered for the canton’s structure plan. As reported on the news portal Nau.ch, these projects were selected from an original catalogue of 29. According to the Cantonal Chancellory, the deciding criteria focussed on aspects such as minimal impact on the landscape and the environment. Another aspect was the fact that the selected projects have their greatest energy efficiency potential during winter. The following options were selected: Griessee, Chummensee, the Oberaletsch Klein region, Mattmarksee, Lakes Moiry and Gornerli, the Lac des Toules upland and Lac d'Emosson. All of these projects are made possible by enabling the use if natural reservoirs created by the receding glacier. The projects’ primary focus is on elevating existing impounding reservoirs or setting up new ones.
Each of the two generators has 2 wings with a span of 11m, and is connected to a float moored to the seabed with an anchor rope.
TRM’s owner-manager, Max Kloger, does not think in terms of quarterly figures. Instead, he is set on securing his familyowned business a sustainable long-term market position.
In Japan, deepdown ocean currents in coastal waters can be exploited to generate energy, as the IHI company and the New Energy and Industrial Technology Development Organisation have shown in a new project. Kairyu is the first plant to take advantage of the Kuroshio current. The machinery is located 50m below the water surface off the southeast coast of Japan. If it were stationed closer to the surface, it would produce more than the 100kW it generates now, but the generator would be in jeopardy from the frequent tornadoes in the area. IHI now intends to install a 2MW turbine near the prototype. The company estimates the ocean currents off the Japanese coasts can be harnessed to produce around 205 gigawatts of power. The efficiency of these systems is excellent at 70 percent.
TRM has been considered the leading provider of castiron pipework and drivenpile technology for many decades. This has earned TRM the reputation of a trusted partner in water management and special civil engineering in Austria and neighbouring countries. Owned by the Kloger family since 2013, the company has recently been turning heads again with the extensive expansion of its brand last year. Besides opening TRM Swiss, an independent subsidiary in Switzerland, TRM also acquired Lower Bavarian provider Frischhut, a traditionsteeped manufacturer of castmolded parts. Both of these strategic moves have opened up new perspectives for TRM. “At TRM we like to think in longterm dimensions. Our acquisitions are anything but reactions to shortlived market trends,” comments Max Kloger, TRM’s ownermanager.
MAIN ACTIVITIES research and development, engineering and design, manufacture, testing, installation, commissioning of inhouse products; maintenance, overhaul, upgrading, refurbishment and modernization of in-house products and products made by other manufacturers Fallerovo
+385 1 3667 499 e-mail: gim@koncar-gim.hr www.koncar-gim.hr
- hydrogenerators up to 300 MVA - references of delivered generators worldwide, compact generators for small hydropower plants
At the end of September 2022, futurezone.at reported that a power line of more than 600 kilometres in length will soon be providing for a significant share of New York City's electricity requirements. The line is to carry electricity from hydroelectric power plants belonging to the Canadian energy company Hydro Quebec, one of the largest hydroelectric power producers in the world. The operators decided to lay the cables entirely underground and under water. Wherever possible, power lines have been routed along the course of rivers, lakes and other waterways. Supplying a metropolis of millions with so much sustainably-produced energy is expected to result in a significant reduction in harmful emissions. The high-voltage power line, known as the Champlain Hudson Power Express (CHPE), is expected to be fully operational by 2026.
Axpo is the largest operator of hydropower plants in Switzerland, Europe's leading distributor of electricity from renewable energy sources, and has now signed a three-year electricity supply deal with the Swiss Steel Group’s Swiss Steeltec plant. Based in Emmenbrücke, the manufacturing plant will solely use Swiss hydropower electricity for the production of its special steels. The agreement demonstrates Axpo’s commitment to playing a central role in the decarbonisation of Swiss industry by way of innovative energy solutions. The agreement also shows how the Swiss Steel Group is focusing on sustainability and green electricity. Despite the Group's emissions already being low compared to the industry average, the deal ensures they will be reduced even further. The Emmenbrücke plant has the smallest carbon footprint in the entire Swiss Steel Group.
Researchers at the Australian National University (ANU) in Sydney have published a study, claiming to have identified about 1,500 locations throughout the country that are favourable to pumpedstorage purposes. According to the authors of the study, utilising this potential could help to reduce Australia’s dependence on fossil fuels. The researchers specifically focussed on sites with an existing reservoir and the potential for an additional reservoir at a different elevation. Australia has set itself the goal of generating 82% of its electricity from renewable resources by 2030. So far, Australia has been considered to be one of the world’s major CO2 emitters, due to its dependence on fossil fuels. Previously, the ANU researchers had already identified another 530,000 possible hydropower sites around the world.
Gugler Water Turbines makes a strategic move into the growing wave energy sector by signing an important cooperation agreement with Exowave. The partnership will see Gugler Water Turbines taking part in the ongoing EUDP project by Exowave “250 MW wave power in the Danish North Sea by 2030 – phase 1” as key provider for the Pelton hydro turbine, including generator and electrical equipment. The agreement will then extend to future projects, in the North Sea at first and on an international scale moving forward. Wave energy is seeing a substantial growth over the past years with increasing support from governments. The EU alone has set very ambitious targets of 1GW of ocean energy installations by 2030 and 40GW by 2050. As such it is key to create a robust and reliable sector value chain, which will be able to deliver on such targets. The strategic partnership between Gugler and Exowave will support to meet above ambitious targets, combining a renowned turbine technology provider with one of the leading wave energy developers.
Electric actuators for hydropower and hydraulic steel structures
Reliable, powerful, robust.
For several decades, AUMA actuators have proved their reliability in automating sluice gates, butterfly valves and gates in weirs, fish ladders, locks, and hydropower plants.
AUMA’s comprehensive portfolio covers torques ranging from 10 Nm to 675 000 Nm offering homogeneous automation schemes throughout the plant: from simple OPEN-CLOSE applications to level control using an integral PID controller.
Discover our comprehensive automation solutions
www.auma.com
LIMBERG 3: POWER STATION’S MOUNTAIN ‘CATHEDRAL’ NOW COMPLETE
With the completion of the cavern for Limberg 3 in December last year, Austria’s largest power station construction site in Kaprun has achieved the first milestone. At 43 metres high, the facility’s machine cavern would be large enough to accommodate one or the other church building. Deep inside the mountain, below the Limberg dam, it took the engineers months of blasting work to excavate the amply sized power station cavern. Measuring 25m wide, 63m long and 43m high, the excavated site is located next to the machine room of Limberg 2. While the concrete pouring work is proceeding inside the cavern, the channels for the turbines’ water supply, the horizontal intake conduit and the pressure shaft are being concrete reinforced and armour-plated. Limberg 3 is a pumped-storage power plant with an overall output capacity of 480MW. Like Limberg 2, which went on-line in 2011, it is being constructed completely underground between the two existing reservoirs of Mooserboden and Wasserfallboden (1,672m maximum storage level).
Hydropower plays a central role in China's electricity generation mix with a share of 14.6%. Older plants, such as the Shilongba power plant in the southwestern Chinese province of Yunnan, which went online in May 1912, still play an important role. What makes this hydropower plant so unique is that it is still generating electricity reliably, partly using the original infrastructure. The generator still bears the emblem of ‘J.M. VOITH Heidenheim, 1910’. Originally, the power station played an essential role in the industrialisation of the region, later powering private buildings. Today, after being expanded several times in the past century, the power plant has four sets of machines with a total installed capacity of 7,300 kilowatts.
The newly-built Dak Di 1 power plant in the Vietnamese province of Quang Nam began generating clean electricity for the first time in November 2022. The Nam Thien Group realised the diversion power plant project to enhance its performance and power generation capacity in the hydropower sector. The operators chose the expertise of the hydropower specialists at GUGLER Water Turbines GmbH to provide the electromechanical equipment. The Austrians supplied two vertical-axis Francis turbines, each designed for a 225.6-m net head and 8.05-m³/s flow rate, and each directly coupled to a synchronous generator. Working at load capacity, each turbine produces over 16.5 MW of bottleneck power. They are the most powerful machines GUGLER has manufactured for Vietnam to-date. The Dak Di 2 power plant is located a few kilometres downstream and was built at the same time as Dak Di 1 and also equipped with GUGLER’s highefficiency Francis turbines. Together, the two new plants provide bottleneck capacity of more than 48 MW.
The socialist Republic of Vietnam has a population of around 90 million, and hydropower-generated electricity is one of the central pillars of the country’s electricity supply. More than a third of the electricity generated in the country is produced using water – a renewable resource. Most of the remaining power comes from coal, natural gas and nuclear energy. At present, less than half of the country’s hydropower potential of around 120,000 GWh per year is being exploited, so Vietnam is one of the most promising hydropower markets in the entire south-east Asian region.
One of the latest hydropower projects in Vietnam was successfully completed in Quang Nam province, in November 2022. The project was realised by the Nam Thien Group, an enterprise commercially active in the energy, industry, real estate and services sectors. The Nam Thien Group began life in the construction sector, before moving to
energy, and now focussing completely on hydropower. Since 2005, the Group has built a whole series of hydropower plants in the Vietnamese province of Lao Cai, and it was involved in the construction of another two hydropower plants in the remote province of Quang Nam, Dak Di 1 and Dak Di 2. Work on these plants, located just a few kilometres apart, started in 2019. They generate electricity by exploiting the hydro-energetic potential of the Thu Bon River.
GUGLER Water Turbines GmbH is an internationally renowned Austrian hydropower specialist, and provided the electromechanical equipment for both power plants. “The contract for the delivery of four Francis turbines, generators and sub-units was signed in May 2020. Two horizontal-axis machines were delivered for the Dak Di 2 plant, each with a bottleneck capacity of approximately 8.5 MW, each designed for a capacity water flow of
12.75 m³/s and a net head of 98.5 m. The Dak Di 1 power plant was equipped with two vertical-axis turbines, each designed for a bottleneck capacity of 16,527 kW at a net head of 225.6 m, and a maximum water discharge volume of 8.05 m³/s,” says GUGLER’s project manager Thomas Berger. He added that the order for the Dak Di 1 power plant had posed an unusual challenge in terms of design engineering: “A head of more than 220 m and comparatively low flow volume combined to pose a significant challenge in terms of the space required for the vertical-axis machines. Great care was taken when engineering the turbines to ensure that sufficient space was available for future maintenance work.” From an organisa-
tional point of view, the restrictions imposed by the Corona pandemic created various hurdles for the project, as Thomas Berger points out: “Around the world, Vietnam was one of the countries with the strictest measures aimed at stopping the spread of the virus. Generally, it was very difficult to obtain an entry permit, and people entering the country had to enter quarantine after arrival.” Weather conditions also posed challenges for the construction company, especially in 2021, when persistent rainfall and subsequent flooding delayed construction progress.
The turbines were manufactured in Europe and transported to Vietnam by sea. The
turbines were delivered in a largely prefabricated state to ensure rapid assembly and installation on the construction site. The turbine spirals, the guide vanes and drive trains, impellers included, were pre-assembled at the manufacturing plant. Essentially, due to the vertical-axis design, installation of the machine groups in the powerhouse was carried out in three steps. Initially, the draft tubes were aligned and set in place. Once the concrete had hardened, the turbine spirals were installed on the level above. Subsequently, another level – on which the generators were located – was concreted above it. “In each case, the on-site installation was carried out by local personnel, and monitored by a GUGLER supervisor. It’s worth mentioning that our supervisor was by no means idle during quarantine, being able to observe the most important installation steps and construction site activities via live images. Furthermore, daily logs of the construction site activity were documented on site, and transmitted to the supervisor.”
The turbine impellers each have a diameter of 920 mm, were milled from forged stainless steel monoblocs and coupled to the generators via separate turbine shafts. “Guaranteeing accessibility to the generator shafts in a vertical set-up means the infrastructure can’t be designed as compactly as with a horizontal machine group. Due to the need for greater distance between generators and turbines, separate turbine bearings were required to ensure vibration-free motion of the turbine runner,” Thomas Berger explains. When manufacturing the turbines, GUGLER relied on proven designs, such as oil-lubricated slide bearings and mechanical seals, to give the operators the greatest possible degree of
• Flow rate: 2 x 8.05 m ³/s
• Net head: 225.6 m
• Turbines: 2 x Francis
• Turbine axis: Vertical
• Ø Runners: 920 mm
• Nominal output: 2 x 16,527 kW
• Manufacturer: GUGLER Water Turbines
• Generators: 2 x Synchronous
• Voltage: 10.5 kV
• Frequency: 50 Hz
• Nominal output: 2 x 17,400 kVA
• Manufacturer: Gamesa Electric
reliability. Each machine group was equipped with cooling units to ensure an optimal operating temperature for the oil-sump-lubricated bearings. Each of the air-cooled synchronous generators, produced by the Spanish manufacturer Gamesa Electric, weighs over 50 metric tons. According to GUGLER’s project manager, Gamesa has proven itself to be a reliable partner over the past few years. The hot air is passed out along exhaust ducts through the intermediate ceiling in the machine building. The identical machines are also equipped with slide bearings, each being designed for 10.5 kV operating voltage and 17,400 kVA nominal apparent power. GUGLER’s scope of delivery also included the main inlet butterfly valve, and the hydraulic units for the turbine control infrastructure. Electrical and IEC equipment, such as the medium-voltage switchgear, auxiliary power transformers and the diesel-powered emergency generator, were provided by a Vietnamese company. GUGLER specified the machine control logic to guarantee maximum efficiency. The power generated is fed via a newly-laid 110-kV line from the power plant to the mains grid.
Dry-run plant tests were carried out at Dak Di 1 and Dak Di 2 in the summer of 2022 and,
as the penstock still had to be completed, official power plant commissioning took place a few months later, last November. Thomas Berger reported a very positive operating experience registered since completion: “Since commissioning, we’ve only had positive feedback from the operator. There have been no system failures or noteworthy malfunctions so far. Looking back, an interesting project was brought to a successful conclusion – despite the challenging accompanying circumstances,
thanks to the good cooperation with the companies and partners on site. At GUGLER we are also pleased to have established our name in Vietnam with higher performance-class machines. Dak Di 1 is the most powerful power plant we have hooked up to the grid in Vietnam to-date.” Project manager Thomas Berger is confident Vietnam will continue to be an important market for GUGLER, as the Austrian industry experts are currently implementing four more projects in the country.
The Makari Gad hydropower project located in Darchula District has successfully commissioned in March 2023, and boasts an impressive set of features. With a gross head of 900m, it is the hydropower project with the highest head in operation in Nepal. The station output is 2 x 5,0MW and the electro-mechanical equipment has been supplied by Wasserkraft Volk AG (WKV), a leading hydropower specialist from Germany.
The project was initiated by a wellestablished company from Nepal and was later joined by two developing partner companies from Sri Lanka. Building the civil works for the project, especially the headworks, penstock pipeline, and transmission line, was no easy task. In particular, the lack of access roads for the complete headworks with heavy rainfall during monsoon and penstock works made transportation of construction materials extremely challenging. The construction team had to transport each cement bag from the powerhouse to the headworks area via ropeways and mules. They even disassembled and reassembled a complete excavator for the headworks. Despite these difficulties, the team completed the project in just two and a half years to an exceptionally high level of quality that can compete with hydropower projects anywhere in the world.
Another unique challenge of the project was the 27km long transmission line. The analysis led to the conclusion that building a 33kV transmission line with poles would be easier and cheaper than a 132kV transmission line, which would require costly towers. Although losses in such a long transmission line at the 33kV level are higher, the use of special conductor ropes with an above-average diameter has helped keep the losses at a minimum.
WKV was contracted to provide the electromechanical equipment for the project powerhouse due to their reputation for delivering high-quality, reliable equipment. WKV is the only supplier manufacturing turbines and generators under one roof in Germany and can grant a warranty of 5 years. The turbines, generators, governing system, and control system, including the SCADA system, were all manufactured by WKV in Germany, providing unique advantages and benefits for the customer in terms of operation and maintenance. The customer has already been operating other hydropower plants with WKV equipment for more than 20 years and can attest to the fact that power generation is consistent even after 20 years of operation. This has led to profitable investments and ensured maximum energy generation within the limited PPA period in Nepal.
The Makari Gad project demonstrates WKV‘s expertise across its product range in Nepal. WKV installed two low-head Francis turbines with only 35m head in another Nepali project, which has been in operation since
• Flow Rate: 1.35m ³/s
• Gross Head: ca. 900m
• Turbines: 2 x Pelton
• Rotation Speed: 2 x 1,000rpm
• Maximum Output: 2 x 5,100kW
• Manufacturer: Wasserkraft Volk AG
• Generator: 2 x Synchronous
• Voltage: 2 x 6,6kV
• Frequency: 50Hz
• Maximum Output: 2 x 5MW
• Cooling System: Air
• Manufacturer: Wasserkraft Volk AG
• Average Annual Production: ca. 70GWh
2022. With Makari Gad, WKV has now put into operation a project with an extreme opposite head of 900m and a discharge of both turbines of only 1.35m³/s. Although the Nepalese market is large, it is also challenging, but WKV has been a leading player in the market for over 20 years. WKV entered the Nepalese market 20 years ago and worked with a Nepalese company on the first hydropower project in Nepal, realised by a private investor.
Makari Gad is proof that when real specialists work together, outstanding results can be achieved. Hydropower is an investment business, and the profitability of this business depends primarily on the reliability of the E&M equipment, which generates energy for the next few decades. Therefore, it is crucial to install only the best possible equipment to achieve the highest profitability of the investment.
In a way, it was the idea of killing several birds with one stone that inspired the latest process water project at the Stilfser Joch national park in South Tyrol in the Italian-Swiss-Austrian tri-border region. Based on a complete redesign of an existing power station on the Suldenbach by the local EnergieWerk-Prad cooperative, the project also included plans to renew the existing overhead irrigation system, install an all-new drinking water pipeline, and even provide a new bicycle trail up the Stilfser Joch. Around €11 million of the €20 million project went towards the new construction of the Suldenbach hydropower station. Equipped with a new Pelton turbine, the new green-power station has an annual output of around 21GWh – three times the amount achieved by the old facility.
It was its unique machine equipment that made the old Mühlbach 1 power station stand out among other facilities of its kind. Where else would you find a power house where a Francis, a Kaplan and a Pelton turbine working together under the same roof?
“We used to love to show this arrangement as part of our guided tours. It was a great opportunity for visiting school classes to get an object lesson on our region’s three most prominent types of turbines,” says Mag. Michael Wunderer, managing vice chairman of the EnergieWerkPrad cooperative, which was founded 100 years ago to foster local hydropower development. Today the cooperative operates a 120km mediumtolowvoltage
grid, which provides its customers and members with green electricity. It is generated primarily by four hydropower stations and four heatandpower plants. One of the four smallscale power stations was the Mühlbach 1 facility. Originally built in the early 1980s, it has now been successfully renewed and expanded.
Someone knew all along that the Mühlbach 1 facility had the potential for extensive enlargement: energy pioneer Georg Wunderer, a local from the Vintschgau region. The uncle of today’s managing director and chairman of
the energy cooperative for 40 years, Wunderer was a keen promoter of the guiding principle, “Energy from local sources”. The extension of the Mühlbach 1 power station had always been a matter very close to his heart. After many years of preparation, including a legal dispute with a competitor for the project, the province of South Tyrol finally granted official permission to the EnergieWerkPrad cooperative in the summer of 2018. Wunderer, the main driving force behind the project, still lived to hear the great news. He died later that year.
Strictly speaking, the existing hydropower station was a twin facility, as the three installed machine units were fed by two pipelines. As
Walter Gostner, a planner from the engineering office of Patscheider & Partner, explains, “A Francis and a Kaplan turbine were installed in the early 1980s. This was state of the art at the time to utilise the available water volume. Compared to this new facility the head was much lower – about 20m – although it was possible to utilise 4,500 litres per second. The Pelton machine unit was added in 1987 along with the overhead irrigation system, which was also used for power generating purposes.” The main difference compared to the new project consisted in the use of a separate turbine penstock and an irrigation line that worked independent of the hydropower facility. This is why the new plan called for the installation of an allnew DN1200 penstock with a total length of 3.3km. “Based on our initial efficiency audit we knew from the start that this project held a considerable synergy potential,” says Wunderer. As a result, the original hydropower project was expanded step by step
into a multipurpose project that is now considered an exemplary model.
Besides an improved irrigation quality, the drinking water supply is another essential synergy effect that benefits the residents of Prad. The municipality had been struggling to ensure the proper quality of its drinking water, as Michael Wunderer recalls: “For Prad the project has opened up an opportunity to utilise new, abundant sources of highquality drinking water in our neighbouring community of Sulden. This will ensure a proper supply of drinking water for years to come.” However, that is still not all. As it turned out, it was possible to develop yet another synergy potential, this time in cooperation with the municipalities of Prad and Stelfs, the local tourist association, the national park, and local council offices: a dedicated bicycle trail leading up the Stilfserjoch mountain saddle. “The
Stilfserjoch road is one of the highest mountain pass roads in the Southern Alps, and it had a notorious reputation among cyclists, as they had to share the road with all the other vehicles. Now it was finally possible to build the first section of a separate bike trail along the pipe route, which is closed to other vehicles. The official opening is planned for the very near future. The next section will be completed as part of a followup project,” as Wunderer explains.
The power station’s entire water intake was completely renewed. The intake construction consists mainly of a weir field with a steel manufactured fishbelly gate and lateral intake, a gravel guard, and a double sand trap. The latter was implemented using the modern HSR desanding system, which enables an uninterrupted operation of the power station without the need for intermittent flushing. It was provided by South Tyrolean hydro steel specialist Gufler Metall of Moos im Passeiertal. They were contracted to provide most of the hydraulic steelwork construction for the water intake. The only exception was the horizontally aligned trash rack cleaner, which was subcontracted to hydraulic steelwork and machine engineering specialist Wild Metal of the town of Ratschings. Their horizontal trash rack cleaners enjoy an excellent reputation in the industry for their exceptional reliability. Delivered straight off the production line at Gufler Metall, the steel manufactured, 12m wide weir baffle is operated sideways by means of a hydraulic cylinder to ensure a constant water level at the weir gate. The steelwork specialists from the Passeier valley also provided the gravel passage lockgate with attached
debris flap, the 6m wide intake gate, and the pipe burst valves for the penstock and irrigation pipeline. It was also Gufler Metall who made another essential contribution to the project: “During the first year of operation we noticed that the water from the overhead irrigation was rather clouded, and small twigs and leaves were passing through the finegrated rack that has a gap with of 1.5cm. So we had to step in and fix that,” says Walter Gostner. Gufler Metall was contracted again, this time for the installation of an additional Coanda screen. It is very efficient in keeping small floating debris away from the pressure chamber of the overhead irrigation system. The screen is also selfcleaning, which means it is virtually maintenancefree.
Unlike the intake construction and penstock, the existing power house was not replaced completely. Instead, it was elaborately hollowed out and modified to accommodate a single cuttingedge machine unit. This was because a
• Design flow rate: 1'980l/s
• Turbine: 4-nozzle Pelton
• Rotation speed: 500rpm
• Generator: synchronous
• Hydraulic steelwork: Gufler Metall
• Weir flap: width 12m
• Outlet sluice: w: 1.7m h: 2.5m
• Trash rake cleaner: horizontal
• Penstock material: steel
• Planning: Patscheider & Partner
• Commissioning: June 2022
single 4nozzle Pelton turbine with directly coupled synchronous generator was to replace the three different machine units. As for the electromechanical and secondary equipment, the operators opted for technology by longstanding South Tyrolean specialist Troyer. The machine they provided was custom tailored to maximise the energy output of the Suldenbach facility. With an effective head of 173.4m and a design flow rate of 1,980l/s, the machine achieves an installed capacity of 3.0 MW. Thanks to the new machine unit, the EnergieWerkPrad cooperative was able to achieve the quantum leap in energy production that they had hoped for: “With the old Mühlbach 1 power station we’d barely ever got above 7GWh a year, but the new facility now generates about three times that – 21GWh”, says Wunderer with a smile. For him and the energy cooperative this achievement represents a crucial milestone: “With all our facilities taken together we now generate between 30 and 32GWh of energy. Thanks to this boost in
• Net head at Qmax: 173.4m
• Manufacturer: Troyer
• Average capacity: 2.99MW
• Design capacity: 3.8MVA
• Desanding system: HSR
• Dam height: 1.5m
• Inlet sluice: w: 7.5m h: 1.0m
• Manufacturer: Wild Metal
• Length: 3'300m DN1200
• Controls & regulation: Troyer
• Average annual output: 21GWh
capacity we’re now able to supply our customers with local energy all year round – even during the winter season!”
Overall, it took the engineers a little more than six months to refurbish the entire hydropower station. In June 22 it was finally time to take the new machine unit online. The facility has been running smoothly, reliably and efficiently ever since. As for the other synergy projects, they have not all been completed so far. Although the irrigation system was already taken into operation last year, the new drinking water pipeline in Prad is still under construction. Walter Gostner expects Prad’s residents to receive most of their drinking water via the new supply pipeline once it is finished. The new uphill bike trail is planned to be opened to the public in late spring this year. Together with the other parts of this comprehensive multipurpose project, it will be presented to the public and given a proper opening ceremony.
The complete rebuilding of the Jettenbach-Töging Inn power plant in Upper Bavaria involved an investment volume of around €250 million, making it Germany’s largest hydropower project in the last few years. The VERBUND Innkraftwerke GmbH project encompassed the complete rebuilding of the weir in Jettenbach and machine house in Töging, each next to the original listed structure. The concrete seal of the around 20-km diversion channel at the plant, originally installed between 1919 and 1924, had to be raised by 70cm due to the required rise in the reservoir head. This renovation resulted in an annual energy production rise of about 25%, so the power plant now serves the annual electricity requirements of around 200,000 households on a sustainable basis.
When completed in 1924, the Upper Bavarian Jettenbach-Töging plant was the first hydroelectric power station built on the River Inn, originally to generate electricity for an aluminium plant in Töging. A 6-span weir in Jettenbach dammed up the Inn, storing up to 340m³/s of works water for delivery to the powerhouse in Töging along a diversion canal approximately 20km long. This water drove 15 Francis turbines in the powerhouse to provide a combined bottleneck output at full capacity of more than 85MW. During renovation work on the Inn Canal in 2003, results showed that the smoother concrete applied in the renovation phase had increased flow capacity, suggesting potential for increasing electricity production during the summer months. In 2015, plans for expansion of the power plant, the central parameter of which was an increase in the expansion water volume to 410 m³/s, were submitted to the authorities at the Mühldorf District Office.
“Several plant expansion options were considered prior to submission, including adapting the original machine building. The idea was rejected because it would have meant only very limited plant operation availability for
several years, with considerable power generation losses. In addition, the existing structure is a listed building. This would have made large-scale technical modernisation extremely complicated. By completely rebuilding the power house next to the original building, the
old plant continued to generate power, even throughout the construction phase, until it was finally shut down in September 2021”, explained Bernhard Gerauer, VERBUND’s overall project manager – adding that the approval procedure prior to project implementation had involved considerable effort. A further key aspect of the project was the construction of a new weir around 50m downstream from the previous location. Raising the weir head by 70 centimetres necessitated the extension of the concrete seal back up along the diversion route in the Inn Canal.
The new weir in Jettenbach is made up of four weir sections, each 26m wide and 9m high. The weirs are designed to be rotating segments with flaps attached. When in operation they have to withstand immense physical forces, particularly radial forces generated by the pressure of the water. These are exerted on the bearings positioned on both sides, and passed
onto the structure. The stress amounts to around 6,700kN per bearing, and in the axial direction approximately 1,600kN per bearing. A water-powered screw with near-bottom and near-surface entry points was positioned on the orographic left side of the new weir to serve as a fish pass. “At 16.3rpm, the screw rotates slowly, thereby transporting fish safely down a height difference of 8.8m into the tailwater within a cushion of water. Whenever there’s weir overspill, fish will be able to descend directly over the weir,” says Bernhard Gerauer. The hydroelectric screw conveyor manages flow at 3m³/s, for a bottleneck capacity of about 200kW. In a normal year it can generate around 1.5GWh of electricity. The bypass channel, built as a fish ladder in 2003, was adapted to the new weir‘s target head.
The mechanical engineering sub-project manager at VERBUND, Christian Weichsel-
© VERBUND
braun, reports: “The issue of safety had a major influence on the design of the three vertical-axis Kaplan turbines.” He emphasised that: “Essentially, it was a question of how the machines would be expected to react in the event of grid failures or large-scale blackouts. What would happen if we were no longer able to release the electricity onto the grid? If the guide vanes in the turbines closed within seconds while operating at full capacity, the worst case could see 410m³/s of works water create a backflow wave, leading to flooding along the diversion route. ‘Sailing mode’ was implemented to eradicate this risk. Basically, operating in sailing mode involves the removal of water through the rotating turbine without transferring power from the generator to the grid. To do so, the impeller is completely opened, while flow and speed control are governed by the guide vane. The braking force of the open impeller generates a speed increase of up to 120% of nominal speed. Energy potential is dissipated by pressure pulsations in the turbine caused by vortex formation in the bladeless space between the impeller and the guide vane. “The turbulence triggers strong vibrations and immense stress forces, especially on the suction pipe, impeller, shaft, lower turbine guide bearing and turbine cover. The machines had to be constructed and designed to ensure no damage would occur in such event,” outlined Christian Weichselbraun, adding that during commissioning the testing of all three machines was completed in sailing mode over a period of ten hours without any problems.
The Slovenian manufacturer Litostroj Power manufactured three double-regulated Kaplan turbines for the project. All three of the
• Flow rate: 410m³/s
• Net head: 35,5m
• Turbines: 3 x Kaplan
• Axis: Vertikal
• Rotation speed: 3 x 166,7rpm
• Output: 120 MW (combinded)
• Manufacturer: Litostroj Power
• Generators: 3 x Synchronous
• Output: 3 x 55MVA
• Cooling System
• Manufacturer: Voith Hydro
• Annual average production: ca. 700GWh/a
turbines were identically built, and designed for a maximum water flow capacity of 136.7m³/s from a 35.5-m net head. Working at full capacity, each achieves a 46.2-MW bottleneck maximum. Adjustable runner blades and guide vanes enable the turbines to double-regulate and achieve maximum efficiency for a wide range of flow rates; even with a reduced water supply. The 6-blade impellers are manufactured from high-grade stainless steel, rotating at 166.7rpm in modulating mode and increasing to 200rpm in sailing mode. Installation of the respective turbine components was a multi-step procedure linked to construction progress at various sites within the power house. “The intricacy of the relationship between construction and concreting work when installing the electromechanical equipment was generally important for ensuring we kept to the project schedule” the two project managers confirmed. Each of the three machine sets in the powerhouse was fitted with a synchronous generator, directly coupled to the turbine runners, and with a nominal apparent power of 55MVA. Essential electrotechnical equipment, including generator protection and excitation equipment, medium-voltage switchgear elements, low-voltage distribution infrastructure, and the plant’s control technology, was supplied by Andritz Hydro.
One project milestone was reached on 21st September 2021 when the machines that had been in operation for almost 100 years were finally shut down in the old powerhouse. “We’d been working towards this date for years” stated Bernhard Gerauer. “Decommissioning the old machines enabled us to finish the remaining construction work and complete the concreting of the intake area at the new power house.” Excitement began to build a few months later when wet commissioning commenced at the new plant on 1st February 2022, as Christian Weichselbraun explains: “Starting up the machines for the first time was a key moment, as water could have leaked from the structure or the any of the numerous seals. Fortunately, we were spared any major leaks and the start-up was a success.” Over the following months the new plant was tested extensively, and the various ‘teething troubles’ that inevitably occur in a project of this magnitude were eliminated. By mid-June the plant was ready to go into regular operation.
In conversation with zek HYDRO, both of the project managers drew a thoroughly positive conclusion on the project. “We‘d be happy to do it all over again” says Bernhard Gerauer. “We had the luck that goes with hard work. The entire project was completed within the estimated cost and time frame, which is not a matter of course. It’s important and satisfying to note that no serious accidents occurred during the
construction phase.” As Christian Weichselbraun confirms, the success of the project was due to an exemplary team effort. “Cooperation between the VERBUND team, suppliers and construction companies all went very smoothly. Whatever schedule clashes, multiple technical and construction problems came up – they were all solved in a cooperative manner.” The plant commissioning ceremony was held on 30th September 2022, around four years after commencement of initial construction work. Several high-ranking representatives of politics and business attended the ceremony in Töging. In his speech, Bavarian Prime Minister Markus Söder underlined Bavaria’s leadership in the field of renewable energies: “Hydropower is genuine home-grown energy. Here, green electricity is generated for 200,000 households with a-hundred-year-old infrastructure. Bavaria is Germany’s hydropower state, with a total of 4,200 small and large-scale plants generating electricity for four million households. We firmly believe in the value of hydropower and are continually expanding in this field.”
As the EU seeks to meet its renewable energy targets, small hydropower is increasingly gaining attention. However, navigating the EU political processes can be challenging for those in the industry. This article will explore the current EU political landscape and its relevance for small hydro, providing insights into how the industry can engage with European and national policymakers and shape future policies. In response to Russia's invasion of Ukraine, the European response to high energy prices and energy security problems caused the European Commission presented the REPowerEU plan last May. Among other things, it contains proposals for a faster increase in the share of renewable energies in order to quickly replace fossil fuel imports and reduce energy prices. EREF's position is that in order to achieve the REPowerEU goals of decarbonisation and greater energy independence for Europe, all available forms of renewable energy must be used, both from the point of view of increased renewable energy production and better integration of the energy system.
Although small hydropower, with its economic and energy benefits, opportunities and potential for expansion, could help to achieve these goals, the European small hydropower sector remains on the political defensive. With reference to the latest WWF Living Planet Report 2022, environmental organisations are denouncing small hydropower in broad-based political campaigns as environmentally harmful and ir-
relevant to the energy transformation and are calling for a halt to expansion and the dismantling of small hydropower plants. With the intense negotiations on the amendments of the Renewable Energy Directive (RED), the EREF Small Hydropower Chapter successfully lobbied for (small) hydropower to remain eligible for so-called "go-to areas". These "go-to areas" – which should actually be called "acceleration areas" – are areas designated by governments in which a significantly accelerated and, above all, simplified approval procedure applies to renewables. Furthermore, in discussions with the trilogue negotiating team, EREF was opposed to the demand for further restrictions and tightening of the EU legislation that already comprehensively covers hydropower, especially the Water Framework Directive. The Renewable Energy Directive, which has as its objective the development and promotion of these types of energy, must not be used to hinder the continued existence and expansion of (small-scale) hydropower. EREF therefore strictly rejected the European Council's proposal to exclude
hydropower from the provisions of the RED. Already last year, EREF worked successfully to ensure that the negotiating positions of the European Commission and the European Parliament consider the expansion of (small-scale) hydropower to be in the overriding public interest and therefore also suitable for "go-to areas". In parallel, EREF, in cooperation with the Vienna University of Technology, showed in a study that significantly more ambitious 2030 targets for renewables and energy efficiency in the EU are feasible and, above all, economically beneficial. Then EREF introduced a final amendment to the ongoing negotiations. This amendment provides for the Commission to be mandated by the new Renewable Energy Directive to adapt European environmental legislation accordingly and to give priority to renewable energy.
On 30 March 2023, EU legislators reached a provisional agreement on the Renewable Energy Directive (RED III) finalising a long negotiation process. The provisional agreement includes accelerated permitting procedures for renewable energy projects. The purpose is to fast-track the deployment of renewable energies in the context of the EU’s REPowerEU plan to become independent from Russian fossil fuels, after Russia’s invasion of Ukraine.
Member states will design renewables acceleration areas where renewable energy projects would undergo simplified and fast permit-granting process. Renewable energy deployment will also be presumed to be of ‘overriding public interest’, which would limit the grounds of legal objections to new installations. The new legislation text of the RED will be available in late May 2023.
At the national level, small hydropower stakeholders should use the 2023 to lobby ministries of environment, energy and economy for a strong inclusion and expansion of small hydropower in the second National Energy and Climate Plans (NECPs). These plans include, among others, national renewable energy targets and measures for achieving the EUwide 2030 renewable energy targets. National governments submitted their first NECPs three years ago. For the second version, many adjustments have to be made to the now new EU legislation, from which the small hydropower sector in particular can benefit. As with the first NECPs, EREF and its members will analyse the governments' first drafts in summer 2022 and submit concrete proposals for improvement to the European Commission and national governments. The governments should then ideally incorporate these into the final version, which is scheduled for summer 2024.
Another important policy dossier is the new EU Nature Restoration Law, proposed by the European Commission in June 2022, which aims to protect and restore Europe's natural ecosystems. The proposal was announced as part of the EU Biodiversity Strategy and is the first significant addition to European environmental law in more than 20 years. Previously, the Habitats Directive, the Water Framework Directive and the EU Birds Directive as well as the designation of Natura 2000 protected areas were the main instruments of environmental protection. The aim is to strengthen existing EU nature conservation law and to include additional binding measures to restore habitats that have already been destroyed. The Commission has presented the EU renaturation law in the form of a regulation. This means that it will enter into force in the Member States immediately after the conclusion of the negotiations in the European Parliament and the Council. Currently, the European Parliament is still negotiating its position. After that, the Commission, the Parliament and the Council will negotiate the final law in so-called Trilogue negotiations.
As part of the Nature Restoration law, the EU pronounced the goal of having 25,000 km of “free-flowing” rivers in EU countries by 2030. Therefore, the EU will publish a new guidance document in July 2023 that will include, among other things, guidelines for the decommissioning of obsolete barriers. As a result of, among other things, EREF’s contribution to last year’s public consultation, the Commission has agreed to find more beneficial solutions for the small hydropower sector in this regard. EREF, together with other hydropower organisations calls on decision-makers to find a balanced approach to adopt all feasible measures to keep the impact on nature as low as possible and achieve a net positive outcome for the hydropower sector.
The new EU project ETIP Hydropower (9/22 – 8/25) will closely link the EERA Joint Programme Hydropower to the new European Technology and Innovation Platform (ETIP) for hydropower. It succeeds the Hydropower Europe project (2018-2022) which created a forum for more than 600 stakeholders representing all sectors. These stakeholders participated through a program of review and consultation addressing needs of the whole hydropower sector targeting an energy system with high flexibility and renewable energy share. Based on this extensive consultation, the Hydropower Europe Forum developed a Research and Innovation Agenda (RIA) as well as a Strategic Industry Roadmap (SIR), towards implementation of the vision “Hydropower as a catalyst for the successful energy transition in Europe” within the framework of the European Green Deal.
ETIP HYDROPOWER further aligns and coordinates these industry RIA and SIR strategies to provide consensus-based strategic advice to the SET Plan covering analysis of market opportunities and research and development funding needs, biodiversity protection and ecological continuity. Another goal is deepening the understanding of innovation barriers and the exploitation of research results. EREF is responsible for the coordination of and input for working groups, to ensure consistency between ETIP outputs and emerging policy priorities and to disseminate project results to its hydropower network.
The PEN@Hydropower project, which also started in Sept. 22, is an additional networking initiative to bring academic and industrial institutions together to discuss the situation of hydropower, research fields and solutions. The project sets up a network of 51 partners from 33 countries who have a wide variety of expertise needed for establishing sustainable hydraulic power solutions. It organises workshops to coordinate research activities and provides capacity-building through summer training schools. The EU project HYPOSO promotes the European small hydropower industry (equipment producers, project developers and investors) in Africa and Latin America. The HYPOSO Platform is an online Marketing Platform for the small hydropower industry to facilitate business contacts with the stakeholders in Africa and Latin America. Registration is free of charge and registered companies are individually marketed to other members.
When registered on the platform, HYPOSO platform users have exclusive access to the GIS online map with all Hydro Power relevant information and resources (i.e., > 2.000 potential sites) initially for Bolivia, Cameroon, Colombia, Ecuador and Uganda. It also includes early and exclusive information about business opportunities for deployment in the target countries exclusively provided to registered users. EREF and partners of the EU project HYPOSO developed a new handbook on small hydropower. In addition to information on the history and on the application areas of small hydropower, this handbook shows and describes various technical solutions for the small hydropower sector. Valuable information on planning and financing models complete this book.
In October 2022 the University of Notre Dame held a dedication ceremony for their new hydroelectric facility in South Bend, Indiana. Situated on the east side of the St. Joseph river beneath Seitz Park, the 2.5-megawatt facility harnesses the power of the river and is expected to produce about 7 percent of the electricity for campus and offset about 9,700 tons of CO2 emissions annually.
The initial idea to use the dam to generate hydroelectric power goes back to the 1980s. However, up until recently, reviving it was not financially feasible, and too complex. The University of Notre Dame and Voith Hydro needed to work with the Federal Energy Regulatory Commission, Indiana’s Department of Environmental Management, Indiana’s Department of Natural Resources, U.S. Fish and Wildlife, the U.S. Army Corps of Engineers, the city and neighbors to make this project happen. The StreamDiver turbines began delivering electricity to the University of Notre Dame in May of 2022.
The 206-mile waterway was an important canoe route during pre-industrial times as well as an important source of food and raw materials. Its floodwaters helped to enrich the
surrounding soil and contribute to bountiful crops. Later, with the construction of a concrete and timber crib dam and two raceways, it helped to power early industry, including glass and textile manufacturing. This continued into the 20th century, when the river was used to produce hydroelectricity for manufacturing and, later, cooling water for a coal-powered energy plant housed in the present-day Commerce Center. But as industry moved away from the river in search of cheaper and more abundant land, concern for the waterway as an economic asset - not to mention an environmental resource - faded, with devastating consequences. At the lowest point, it functioned as little more than an open sewer, channeling human, and industrial waste downstream toward Lake Michigan. Over time, the east and west raceways were redeveloped, the former as a whitewater rafting course and the latter as a water feature
for the city’s new convention center. The dam became the focal point of a rejuvenated riverfront, with parks, pathways and public art including River Lights, an interactive light sculpture.
On the beginning of the project, Paul Kempf, Notre Dame Assistant Vice President for Utilities and Maintenance and his colleagues came to Voith Hydro in Austria. Using detailed assessments and based on the characteristics of the site, StreamDiver turbines were determined to be best suited for this project. Beside other characteristics of this turbine, Voith Hydro’s comprehensive turbine development know-how and its references from all over the world were also decisive factors.
Tucked neatly beneath Seitz Park, the facility consists of 10 turbines, each with a 250-kilo-
Technical details
• Turbine type: 10 StreamDiver Units
• Manufacturer: Voith Hydro
• Head: 3.17m
• Flow rate: 9.90m3/s
• Capacity: 0,255MW per unit
watt generator and a propeller type runner, stacked two-high across five shafts. Water from the intake tunnels turns the runner, activating the generator and pushing clean, renewable energy up the east bank of the river to campus. The water then flows back to the river at a point just below the dam.
From an operational standpoint, the facility is very much hands off. As water flows into the intake tunnels, it is filtered through a screen, or trash rack, to remove branches and other large debris. Farther along, a second rack removes fine debris, such as leaves. A large arm sweeps the screen to keep it clean. From there, an automated system controls the flow of water to the power house and activates or deactivates the turbines based on water level, which ebbs and floods throughout the year. The turbines use water for cooling and lubrication, avoiding the usage of oil or grease. A bypass tunnel allows
• Shortened project time compared with conventional solutions
• Reduction of construction costs up to 40%
• Easy integration into existing weirs or dams
• Minimal operating and maintenance costs
• Ecologically advantages due to water-lubricated bearings and thus oil and grease-free operation
• Water-flooded generators, no leakage risk
• Submerged installation, low visual and acoustic disturbance
• Can be assembled and disassembled very quickly due to underwater plug and suspension
wayward fish to travel safely up- or downstream through the facility while avoiding the turbines. Should maintenance become an issue, the turbines can be removed and repaired or replaced via a rail system, with no need to dewater the plant.
For its exemplary innovations, products, and services it contributed to the Notre Dame Hydro project, Voith Hydro has been awarded the University of Notre Dame Procurement Partner Sustainability Award. The project is the largest carbon reduction measure implemented to date as part of the University’s goal to become a carbon neutral campus by 2050.
“The turbines and technology supplied by Voith Hydro played an important role in meeting our project’s sustainability goal. These StreamDiver turbines are also the first such installation in North America and will supply a green energy source that we expect to contribute approximately 7% of the campus’ electricity,” says Shannon Cullinan, Executive Vice President at Notre Dame.
By reducing complex technology, it was possible to achieve a compact size and an extremely maintenance-friendly and robust machine unit at the same time, which has gradually established itself on the global hydropower market with worldwide references in recent years. Today, StreamDiver units from Austria to Indonesia, from Macedonia to Brazil prove the efficiency of this approach.
At the Falgu river in the Indian state of Bihar the Austrian Hydro-Construct GmbH finished another notable rubber dam successfully. This was just in time before the beginning of the Hindu festival „Pitri Paksha“ in the second half of September 2022. The Austrian Company designed, delivered and installed the 390m wide air inflated rubber dam. Which is located right beneath the footbridge connecting the Hindu temples of Sita Kund and Vishnupad Mandir in the city of Gaya. As is usual for Hydro-Construct, this 3.10m high six span rubber dam breaks the record for being the largest rubber dam in India. Due to the intensive rainy season in this part of India the installation followed a tight schedule.
Since the beginning of the new millennium Hydro-Construct, based in Steyr, Austria, supplies rubber dams to India. Starting with rubber dams of usual sizes the recent projects shift the size limit for rubber dams to new dimensions. In line with this the Gaya Ji dam sets a new record for being the largest rubber dam in India. Six spans of 65m length and 3.10m height each addup to a total width of 390m. One of the advantages of rubber dams is that they provide the most cost efficient solution for such long flexible weir structures. Since rubber dams have no significant mechanical parts, only reduced maintenance efforts are necessary. In addition they will not pose an obstacle when they are fully deflated in times of flood. The Gaya Ji dam uses an air inflated rubber dam system to create a reservoire in front of the Hindu temples of Sita Kund and Vishnupad Mandir in the river Falgu.
The Gaya Ji dam project is a project of the governement of the State of Bihar and the City of Gaya. As a general contractor NCC
Limited, Hyderabad, India, has been appointed, which also was responsible for all civil works. Hydro-Construct won the bid for the supply of the rubber dam by offering the
technically and economically best rubber dam solution. The rubber membran was produced by the joint partner Rubena, s.r.o., Czech Republic.
For Hydro-Construct it was the first cooperation with NCC Limited. Both companies were eager to make this project a success, also as it was possible to build the whole project during only one dry season and inaugurate it one year ahead of time. NCC project manager Girish Kumar Gopisetti praised the proven onsite team of HydroConstruct under the supervision of the joint
partner AQUATIS a.s., Czech Republic, for its competence and determination, which were the key factors for the projects success. Even though the conditions with temperatures up to 40 °C and sometimes difficult communication were rather challenging all obstacles and difficulties could be eliminated.
The rubber dam is part of a greater project including also a footbridge connecting the Hindu temples of Vishnupad Mandir and Sita Kund, two important pilgrimage sites. Traditionally in the second half of September
during „Pitri Paksha“ tens of thousands of pilgrims make their way to Gaya to visit these temples and perform the „Shraddha“ ritual. Therefore special efforts have been taken to finish the project before the start of „Pitri Paksha“ festival. On Sep. 8th 2022 the Gaya Ji dam was inaugurated by Nitish Kumar, the chief minister of Bihar, in an impressive ceremony. Major governemental officials and thousands of people celebrated the finishing of the works and the unveiling of the inauguration stone. Not only during „Pitri Paksha“ the rubber dam and especially the colorfully illuminated footbridge is an attraction to visitors and locals alike.
Besides its dimensions this rubber dam also features some new developments in rubber dam technology and regulation. For the first time Hydro-Construct installed a six span airinflated rubber dam, where in automatic operation each span could be operated in parallel or serial. An innovative way of connections between the control systems of all spans allows to operate the rubber dam also in groups of connected spans considering several oportunities of redundancy. This increases the resilience and operation safety of the system. Hydro-Construct, in cooperation with the partner ESA GesmbH, Steyr, Austria, also implemented a V-notch bypass control algorithm. This helps to avoid the, especially for air inflated dam regultion, obligatory disturbant of the weir crest contour, which leads to a reduced stability and concentration of flow in limited areas of the whole width. Hydro-Construct also developed a new and patented double clamping rail system, which adds a supporting clamping rail to the upstream clamping rail. This successful project is leading to establish Hydo-Construct India Ltd. which is responsible for the Indian market. The new company is managed by Ram Reddy as Managing Director and Bharath G. Reddy as General Manager.
Hydro-Constructs prospects in India is positively influenced also due to the activities of Hydro-Construct India. In the meanwhile for five future projects Hydro-Construct is now in touch with the possible clients. Because of the successful completion of five projects in India Hydro-Construct is quite confident to be successful. These prospective projects are spread all across India. Hydro-Construct India also acts as a constulting and project planing company on the topic of hydropower. India as a growing economy has a huge demand for energy. Renewable energy sources such as hydropower have much potential when working towards the goal of supplying sufficient sustainable energy.
While the Gaya Ji dam is the most recent project Hydro-Construct finished in India, the rubber dam on Gomti river in Lucknow is also a notable rubber dam. With 275m width and 3,2m
height it is also among the largest rubber dams. In contrast to the Gaya Ji dam the rubber dam in Lucknow is filled with water. In terms of stability and regulation accuracy water filled rubber dams are advantagous compared to air inflated rubber dams. The rubber dam on Gomti river gets the filling water from a water tank to ensure that the water is of proper quality (high silt and pollution load in rivers) for filling the rubber dam. Hydro-Construct prides itself for being innovative and providing special solutions and so in Lucknow they implemented navigation locks, on both sides of the river, to allow boating traffic between head and tail water. As lock gates also two rubber dams are used to create the manipulation lock chamber. The navigation locks are operated from an external control room. Although this rubber dam on Gomti river has been completed, its inauguration is still pending.
It was in September 2022 when a small-scale hydropower station in the Styrian municipality of St. Kathrein am Offenegg near Graz, Austria, went online to supply its first clean energy. The project was implemented by Hydro Energy Weizbach GmbH, who wanted to realise the full hydroelectric potential of the local water body for the production of clean energy. Up to 80 litres per second are collected and piped to the power house, utilising a net head of around 210m. Measuring 3,145m in length, the DN350 penstock consists of 50% PVC pipes and 50% ductile cast-iron pipework, both provided by Upper Austrian-based Geotrade Tiefbauprodukte GmbH. Inside the power house, a horizontally aligned 2-jet Pelton turbine works in combination with a directly coupled synchronous generator to ensure maximum efficiency. Despite the Corona pandemic and the challenging conditions caused by it, the engineers were able to complete the project successfully within about one and a half years.
First plans for setting up a small-scale hydropower station on the Weizbach rivulet in the small community of St. Kathrein am Offenegg were drawn up in 2015. It was only a year later that the project received the required environmental and official authorisation. Hydro Energy Weizbach GmbH was founded to manage the legal framework. However, the project – although given the official green light – remained on hold for several years. When it was finally completed in the summer of 2022, it was taken over by property developer Hartwig Warmuth. Besides his property development activities, the new owner is also an avid promoter of renewable energies. His photovoltaic facilities are installed throughout Carinthia and achieve a total output of around 2,500 kWh. In addition, Warmuth now operates
two small-scale hydropower stations, including the new Weizbach facility.
“Project optimisation work was kicked off in late 2020. This included both the water intake and the power house, and a realignment of the penstock. In 2021 it was time to go ahead with the actual construction,” explains Ernst Hackenberg, the project’s planner who is responsible for its final implementation. “The installation of the penstock,” he adds, “was done in close cooperation with the Styrian road administration. This was essential, as
there was about a kilometre and a half of country road being built right along the power descent. Although this delayed things somewhat, it absolutely made sense from a logistic point of view.”
The new water intake was fitted with a hydraulically operated weir baffle, the inflow point being equipped with a horizontal protective screen with a clear bar spacing of 10 mm. The floating debris caught by the screen is transported to the weir baffle, where it is either removed manually or flushed out into the tailwater by lowering the sluice gate. Once it has passed the protective screen, the motive
water is collected in a sand trap to let the finely grained sediments settle. The collected sediments are then discharged into the residual water stream via a flushing gate, which is controlled automatically by two sediment sensors in the sand trap. A near-natural pool pass at the weir gate ensures the required ecological compatibility of the water passage.
A PENSTOCK COMPOSED FROM PVC AND DUCTILE CAST IRON
The size DN350 penstock that connects the water intake to the power house has a total length of 3,145m. Two different pipe systems
• Hydrographic Basin: 3,48km ²
• Flow Rate: 80l/s
• Gross Head: ca. 210m
• Penstock: 3.145m
• Ø: DN350
• Material: PVC/Ductile Cast Iron
• Distributor: Geotrade Tiefbauprodukte GmbH
• Turbine: 2-nozzle Pelton
• Rotation Speed: 1,500rpm
• Nominal Output: 140kW
• Manufacturer: Maschinenbau Unterlercher
• Generator: Synchronous
• Voltage: 400V
• Nominal Output: 150kVA (H-B)
• Manufacturer: EME
• Annual Average Production: ca. 600.000 kWh
were used in its construction: “The upper section consists of PVC pipes with a PN16 pressure rating. The lower half is made from cast iron pipes to withstand the higher pressure conditions,” as Hackenberg explains. All basic materials, including the elbows and special cast parts were provided by Upper Austrian distributor Geotrade Tiefbauprodukte GmbH. The upper section is based on System TOM® PVC-O by Spanish-based provider Molecor. The pipes are made of highly durable PVC, the result of a special manufacturing process. This provides high levels of resistance against impact, highpressure pulses and environmental effects to ensure a long lifecycle. Used in high and medium-pressure applications and drinking water facilities all over the world, the system is favoured for its low weight and superior value for money. The penstock’s mid-point marks the transition to the ductile cast-iron pipes for the lower section. They are from Geotrade’s GEOCAST product line, which provides diameter sizes up to DN1000. Known especially for their durability, the pipes easily withstand the higher pressures. A cement mortar coating makes their inner surface extra smooth to ensure optimum flow conditions and protection against corrosive effects. Additional qualities
include a high level of static stability under load, resistance to fracture as well as longitudinally stable joints which, depending on their dimension, allow the pipe ends to bend by up to 5 degrees inside the coupling sleeves. Except for a traverse in the form of a pipe bridge across the rivulet, the entire power decent is routed underground. A data cable laid along the penstock provides a digital link with the water intake.
Inside the power house advanced hydropower technology ensures efficient power generation. The core of the facility is a Pelton turbine with two electrically controlled nozzles. Designed for a flow rate of 80l/s and a gross head of 210m, the machine has a bottleneck capacity of 140kW under full load. The twin-nozzle design ensures efficient operation within a wide partial-load spectrum at times when there is less water available. Although the original plans had called for an air-cooled generator, the engineers eventually opted for a less noisy water-cooled machine to meet the demands of local residents. The synchronous generator was manufactured by German-based EME Elektromaschinenbau Ettligen GmbH. The
high-speed engine is coupled to the rotor and, like the turbine, runs at a rotational speed of 1,500rpm. It is designed for a voltage of 400V or rated apparent power of 150kVA (H-B). A modern control unit provides fully automated control of the entire facility, including a wide range of remote control options, thanks to a secured on-line control connection. Using an underground power line, the energy generated by the facility is fed into the public grid, which is operated by Energie Steiermark, via a transformer station located around 70 m away from the power house.
About a year and a half after the official ground-breaking ceremony, the Weizbach hydropower station came oline in September 2022. “Despite the challenging circumstances surrounding the Corona pandemic we were finally able to bring the project to a very successful completion. Due to the dry weather during the first year of operation, the facility hasn’t been able to make full use of its design capacity so far. That said, it has been running without interruptions since autumn 2022,” says Hackenberg. In a normal year, the new power facility on the Weizbach is expected to generate around 600,000 kWh of green energy.
Having been cancelled in 2020 due to the pandemic, the Viennahydro celebrated its international hydropower event comeback from 9th – 11th November 2022. A most welcome return within this format was made by the ‘International Seminar on Hydropower Plants’, a feature that has offered a top-class science and technology portfolio for over 40 years. Once again, around 230 participants from 20 countries contributed towards ensuring the Viennahydro lived up to its reputation as a highlight in the hydropower event schedule. This year’s show slogan – Hydropower for Future Generations – placed the focus of the event on key issues for the future, such as digitalisation, smart grids, quantum computers and all kinds of innovative trends.
From the 9th – 11th November, after a wait of four years since the previous edition of the fair, held in 2018, the Viennahydro finally returned, welcoming guests to a venue firmly associated with the event – the conference centre at Schloss Laxenburg on the edge of Vienna – which for the three days became the international hydropower industry hub once again. A premiumquality conference programme consisting of 64 specialist talks, and 12 presentations given by prospective doctoral students, ensured the event lived up to the high expectations. There was particular excitement surrounding the panel discussion held straight after the opening ceremony: ‘Sustainable supply availability via renewable energy systems’. Highprofile guests
from the worlds of politics, the energy industry and EControl authorities participated in the discussion. Essentially, despite differing positions and approaches, the exchange of opinions showed that all sides identified very similar issues and findings, and drew similar conclusions. Discussion then moved from a broader perspective to more specific issues, and questions were dealt with in greater detail.
This event is rich in tradition and takes place every two years. Prof. Dr.Ing. Christian Bauer, Dean of the Faculty of Mechanical Engineering and Management Sciences at the Technical University of Vienna (TU Wien), has been involved in the show since 2008. He and his team are the driving forces behind the event. The dean believes the international character of the Viennahydro is an important
factor in its success: “The Viennahydro is an ideal platform for quick and easy exchanges on the issue of hydropower. In Austria, the community – educational institutions such as universities, manufacturers, operators and consultants – is a closeknit network; these benefits are transferred to an international arena via the conference.” The Viennahydro is a unique opportunity to present scientific research to the public, and expert audiences –especially for international doctoral students. It’s hard to imagine the opportunities for international networking being more favourable anywhere else.
As usual, the best possible use was made of the premises at Laxenburg palace; the individual items on the schedule being generously divided between three halls. The afternoon of
day 1 was given over to more practical approaches to the provision of small-scale hydropower, a thoroughly original gender debate in hydropower, to questions concerning operation and maintenance, and to the increasingly important issue of ecology. This first day was rounded off by a sophisticated evening cocktail reception in the historic surroundings of the Vienna City Hall, providing a chance to marvel at an example of Vienna’s rich architectural history, while the vast majority of participants seized the unmissable opportunity to socialise and cultivate contacts.
The prevailing topics on day 2 included the central and ever-relevant issue of pumped storage, as well as control and automation, operation and maintenance, hydraulic systems and transient conditions, digitalisation – and numerical simulation. The main theme of the event picked up on the common thread: ‘Hydropower for Future Generations’. The organisers of the Viennahydro were clear about the need to pose the right questions regarding the future uses of hydropower. Specifically, the dean, Mr. Bauer, said: “Storing energy and then feeding it back onto the power grid at a high level of efficiency is a major challenge. This is an area in which we aim to provide support. Rather than building new infrastructure, it’s a matter of exploiting existing infrastructure – such as reservoirs. In Salzburg there are examples of untapped potential. Artificial reservoirs used to serve snow cannons are not used for about 11 months of the year. New developments like modular pump turbines can help energy to be stored in a decentralised manner, without requiring new power lines to feed it back onto the grid.”
On day 2 the intensive discussions and expert talks went on throughout the evening meal, held in an extremely cosy atmosphere. As has been the custom for many years, the second day of the event was rounded off with a visit to the
traditional Fuhrgassl-Huber wine tavern in Neustift am Walde. This side-event is sponsored by the hydropower all-rounder Voith Hydro, and become one of the secret socialising highlights offered at the Viennahydro. The informal tavern environment guarantees an ideal atmosphere for networking. As always, the professional conference environment provided a stage upon which several sector insider companies were able to introduce their products and services to well-known ‘key players’ in the hydropower industry. Many come to the Viennahydro to make new contacts, and to gather information on the latest developments.
The final day was dominated by the major topic of operation and maintenance; the second part of the day by pumped storage. As the last of a wide variety of fascinating presentations was completed, the 21st edition of Viennahydro drew to a close – proving yet again that the success of an industry event stands and falls on the quality of its content. A committee of almost 40 members guarantees that the standards set by the Viennahydro remain eminent, and ensures only papers reflecting lofty academic standards and sophisticated innovations are admitted at the event. As every year, the dean – Christian Bauer – and his team invest a great deal of effort and detail into preparing the event. The success of this year's event laid the foundation for the next edition of the Viennahydro, which is to be held for the 22nd time in November 2024. It’s a date to be underlined in the diaries of all those around the world with an interest in hydropower. For more informations please visit: www.viennahydro.com
Have an old Francis Turbine?
Since December 2022 the Grandvalira ski resort in the principality of Andorra has been utilising the hydropower potential of a mountain stream to generate clean energy. Within about six months, a new small-scale hydropower station was constructed on the Riu dels Pessons river in the resort’s Grau Roig sector. A water intake that had previously only served for the production of artificial snow was completely rebuilt to supply the required 450l/s of motive water. The entire electro-mechanical and secondary equipment for the power house was provided by Ossberger, a Germany-based specialist for small hydropower. To ensure reliable power generation, the operators opted for a crossflow turbine with a bottleneck capacity of 296kW, which utilises the varying water supply levels to achieve a maximum of efficiency. In a normal year, the new small-scale hydropower station generates around 500,000kWh of green electricity.
For the approximately 79,000 residents of Andorra, the principality between the borders of France and Spain, hydropower generation is of crucial importance. Almost a quarter of the electricity produced in Andorra is sourced from hydropower. Approximately an additional 15 per cent of the annual power requirement come from other renewable resources, such as wind, solar or biomass energy. One of the country’s most recently completed hydropower facilities went on line late last year in the ski resort of Grandvalira, one of the largest of its kind in the Pyrenees, providing around 200km of slopes.
“As in any ski resort, energy is one of the largest cost factors in Grandvalira. And we expect the demand for energy to continue to rise in the foreseeable future. To promote local energy autonomy, Joan Viladomat, who owns Grandvalira’s associated ski areas of Pas de la Casa and Grau Roig, has been researching the possibilities of boosting the resort’s overall energy autarchy,” says Ferran Huertas Martínez, the Grandvalira resort’s deputy technical director. A study was conducted in 2020 to determine the hydropower potential
and viability of energy production in the Grau Roig area. The energy source utilised by the new smallscale hydropower station is the region’s Riu dels Pessons mountain stream. Official planning permission for the site was granted already in autumn 2021. But with winter approaching fast it was clear that the project could not be completed that year, and so the kickoff was scheduled for the following summer.
The power station’s functional design is based on a classic diversion concept, where the motive water is removed from the stream at the intake and routed to the power house via a penstock. The water intake at Grau Roig is located at the site of a former weir gate struc
ture about 2,200m above sea level, which had previously only served for making artificial snow. With the hydropower project the production of artificial snow and green energy are combined. The formerly unused hydroelectric potential of the altitude difference and the motive water serves now to drive the turbine in the power house. After that the water is routed to the existing pump station and is used for the production of artificial snow. Before work on the power station could begin, it was necessary to completely rebuild the water intake and put up the power house. To provide an ecologically compatible water passage at the intake, a fish ladder in the form of a technical verticalslot pass was installed to allow aquatic wildlife to pass through to the headwater area. Another new construction was the 450mm dimensioned penstock with a
• Flow Rate: 450l/s
• Gross Head: ca. 96m
• Net Head: ca. 80m
• Turbine: Crossflow
• Rotation Speed: 1,000rpm
• Maximum Capacity: ca. 296kW
• Manufacturer: Ossberger
• Generator: Synchronous
• Voltage: 400V
• Nominal Output: 306kVA
• Cooling System: Air
• Manufacturer: Marelli
• Average annual production: ca. 500,000 kWh
length of 757m. Consisting exclusively of cast iron pipes, the power descent runs underground all the way, being routed in line with the penstock where possible. As Huertas explains, the high altitude posed a considerable challenge for the project’s engineers: “Obviously, having to work at altitudes of more than 2,000m in a secluded area can make things a bit difficult. Construction work began in June 2022. We knew from the start we couldn’t afford any delays, as work at the construction site would be impossible under snow conditions in winter. Fortunately, we didn’t encounter any significant problems like floods or difficult geological conditions.”
The electrohydraulic components and automation equipment for the power house were provided by Germanybased allround hydropower specialist Ossberger. The technology package from Ossberger was completed by the bypass including a plunger valve for the machine unit. Designed for head heights between 2.5 and 200m, the durable crossflow
turbine is the facility’s core element. The machine is based on a simple design with only three movable parts. Its energy generating performance is highly reliable, as is its ability to cope with fluctuating water volumes. All this is made possible by the turbine’s internal design, which consists of two independently operated cells. As little as 5 per cent of the design flow rate is enough for the smaller cell to drive the turbine. For the Grau Roig power station, Ossberger provided a machine that is optimised for a design flow rate of 450l/s and a head of 96m. Especially in spring, when the snow is melting and the available water volume reaches its maximum level, the turbine can provide a bottleneck capacity of 296kW. A directly coupled synchronous generator transforms the runner’s kinetic energy into electricity. Like the turbine, the aircooled generator rotates at 1,000rpm. The unit is designed for 400V and a rated apparent power of 306kVA. To complete its order, Ossberger also provided the entire electrotechnical and secondary equipment, which ensures the fully automated operation of the entire facility.
After about six months of construction, the pictureperfect hydropower station was finally taken into operation in midDecember 2022. However, it was only able to generate energy for a few days, as the available water volume fell considerably during the cold winter months. Three months later, in MidMarch 2023, the facility could be taken back on line. “So far we haven’t been able test the facility under full load, but we are very happy with what we’ve seen so far. The crossflow turbine by Ossberger is performing brilliantly, and it’s coping well with the fluctuating water supply at this site,” says Martínez. In normal years, the new greenpower station is expected to generate about 500,000 kWh of clean energy. Thanks to the new hydropower station and multiple solar panels mounted on roofs throughout the region, the resort is now able to generate about 10 per cent of its required energy supply. As Huertas is pleased to mention, the ski resort is planning to increase its utilisation of sustainable energies, including water, wind, and solar power, in pursuit of its goal of full energy autarchy.
The massive glacier melt this year has clearly shown us the major changes high alpine glaciated areas are subject to. The retreat of the glaciers is exposing ever larger alpine areas, from which sediments enter the streams and thus the water intakes of the power plants during precipitation. These suspended sediments in the drive water of the hydropower plants cause massive hydro-abrasive wear on exposed turbine components. A decrease in the turbine efficiency and rising operating costs due to more frequent and more extensive maintenance work are the consequences (Abgotspon et al., 2022). In order to be able to minimise this damage, suspended sediments monitoring is required, which not only measures the concentration of suspended sediments, but also provides information on the size distribution of the suspended particles [Abgottspon et al. 2016].
Kraftwerke Mattmark AG operates a hydroelectric power plant in Stalden VS/Switzerland with two machine lines, each consisting of two Pelton turbines, with a total output of 185,000kW. The catchment area of the power plant is mostly located in areas influenced by glaciers. For this reason, Kraftwerke Mattmark AG have agreed to install a new measurement system to record the concentration of suspended solids and their size distribution as a pilot project in spring 2022. The aim is to be able to discharge the inflowing water directly at the water intakes in the case of very high concentrations of suspended solids and, at the same time, to be able to immediately turbinate the water again as soon as the concentrations of suspended solids decrease.
The measuring principle behind the multifrequency echo method is based on the backscattering and attenuation of ultrasonic waves on particles carried in flowing media. In the pulse-echo method, an acoustic impulse is sent into the medium and the intensity of the backscattered signal is measured. This process is repeated with different frequencies emitted by a total of 4
acoustic transducers (Fig. 2) to obtain scattering signals from particles of different sizes. The aim here is to obtain the average and standard deviation for the backscatter coefficient and the effective attenuation of the ultrasonic wave by the medium. Particle concentration and size class distribution (PSD)
are then determined from these parameters using complex mathematical equations. The system can measure up to a maximum suspended solids concentration of 6000mg/l without calibration. Concentrations greater than 6000mg/l are detected, but can no longer be determined accurately due to the
multiple scattering effect. Therefore, only a qualitative measurement can be carried out for SSCs > 6000mg/l. However, in order to reduce the measurement uncertainty at higher concentrations, a calibration curve from laboratory measurements with representative sediment samples can be stored in the system.
The particle size is specified in five size classes: <63µm, 63 – 100µm, 100 – 200µm, 200 –400µm and 400 – 1000µm.
The sensor can be installed directly in the channel or pipe and does not require any complex installation e.g. using a bypass and/or pump control. In addition, the operation of the sensor is largely maintenance-free.
In Saas-Fee, the sensor was installed directly in front of the inlet screen of the water intake in the channel of the mountain stream Saaser Vispa during low water in February 2022 (Fig. 1). Consequently, an alarm can be triggered if a threshold value of 4000 to 6000mg/l is exceeded and the water can be discharged in a controlled manner. At the same time, the drop-in sediment concentration can be detected in real time so that when the concentration is low enough, the volumetric flow can be rerouted back to energy production without causing damage to the turbines. The sensor was installed in a way so that the ultrasonic signals are emitted into the water in downstream direction thereby avoiding any possible damage to the ultrasound transducers by flotsam or debris impact. In order to protect the sensor further sensor housing and cables were shielded with solid steel plates by employees of the Kraftwerke Mattmark AG. Turbulences that occur behind the sensor
Advantages of the system:
- Easy installation without bypass or pumps
- Resolution of size distribution
- No calibration
- Maintenance-free
protection in the sensor’s field of view do not influence the measurement. In addition to the ultrasonic transducers pressure probes were also integrated into the sensor housing for level measurements. Level data is not required for SSC measurements, but it supports the subsequent data evaluation. The measuring transducer was installed 60m away in the control room. From here, the particle concentration, water level and water temperature are transmitted to the control system of Kraftwerke Mattmark AG via analogue signals. The system was commissioned in July 2022.
The following analysis refers to data recorded between 29 July and 1 October 2022. In addition to the data from the particle concentration measurement system, which also records the water level and water temperature in addition to SSC and PSD, flow data from the Stalden hydropower plant were also included for further analysis. Fourteen events featuring a SSC >4000 mg/l occurred during this period. Two of these events had a duration of more than one hour (average: 29 min, median: 17 min).
An initial evaluation of the data reveals periodic fluctuations of all measured values during the course of the day. Due to very high temperatures and very little precipitation, the summer of 2022 was characterised by massive glacier melt. Thus, the increases and decreases in flow over the course of the day can be clearly seen, which, as expected, are accompanied by an increase and decrease in suspended sediment concentration (Fig. 3 and 5). The transport of coarser particles (fine sand and medium sand) increases with higher flow velocities (cf. Fig. 4 and 6). From 8 September, water temperature and flow decrease. The glacier melt decreases. This means that hardly any fine and medium sand is transported while silt particles dominate the material composition. (cf. Fig. 6).
On 25 August, sediment concentrations significantly above 6000mg/l were measured over a period of approx. 41 minutes (Fig. 8). Thus, these values exceeded the maximum measuring range of the sensor and hence were subject to a significantly higher measurement uncertainty. Nevertheless, it can be assumed that this was an event with the highest detected sediment concentration (>6000mg/l) within this measurement campaign. A closer look at the particle size distribution for this event (Fig. 9) shows the chronological sequence of the individual size classes, starting with silt, followed by fine sand up to 100µm, low concentrations of fine and medi-
- Reduction of hydro-abrasive wear through controlled discharge
- Suspended particles monitoring for efficient turbine maintenance
- Monitoring of (continuous)
reservoir flushing
- Sustainable sediment management
um sand up to 400µm and a relatively large proportion of sand up to 1000µm. This succession of the individual size classes and also the underrepresentation of the size classes up to 200µm and 400µm can be found in all events. Deviating from this, a fraction of 20% was detected on 27 August for the size class up to 400µm and 6% for up to 200µm. This sequence of size fractions within an event contrasts with the observations of a long-term study of hydro-abrasive wear on Pelton turbines at the Fieschertal power plant (approx. 40km straight distance from Saas-Fee). In this study, the d50 parameter of the size-sum distribution curve was determined. The results from this study showed that the d50 value was higher at the beginning of the events (rising branch of the concentration hydrograph) than at the end of the events (falling branch of the concentration hydrograph) (cf. Fig. 7). The reason for this is that for this study the measurement systems were installed downstream of the storage tunnel. As a result, the SSC is influenced by settling and resuspension processes at different water levels during operation of the storage tunnel (Felix, 2017). In the hydrographs of concentration events, additionally (e.g. Fig. 3) a periodic event
Authors:
with a strong, pulsating increase in concentration, combined with a drastic drop in flow, can be seen. This is a flushing process of the screen in the inlet of the water intake. By opening the gate valve behind the water intake, a large amount of water and flotsam, which has collected in front of the screen, is discharged abruptly. This results mainly in the resuspension of particles > 200µm, which had previously settled in front of the water intake (cf. Fig. 10).
The measurement data of this campaign show that during certain events, which are caused by snow and glacier melt, heavy precipitation or also by targeted flushing of reservoirs, large quantities of very small as well as very large particles are transported and led to the turbines. Separation of silt and fine sand (< 200µm) by using a desander is in most cases not possible at economically justifiable expense. However, even small particles cause hydro-abrasive wear on the turbines at high flow velocities and strong flow deflections (Abgottspon et al., 2016). The extent to which the large amounts of sand (> 400µm), as occurred in the event on August 25 (Fig. 9) are separated by the desander can only be determined by measuring the SSC downstream of the desander.
In order to better understand the behaviour of the sand trap at high suspended sediment concentrations, but also to be able to schedule maintenance intervals on the turbines more efficiently, in winter 2023 a second SSC measurement system was installed at the same water intake at the end of the sand trap. In this way, on the one hand, the actual SSC and size distribution of the turbined water is recorded, which in the end leads to hydro-abrasive wear on the turbines. On the other hand, this provides Kraftwerke Mattmark AG with information about the sedimentation behaviour in the sand trap at different inflow rates.
Sebastian Scheffler, Nivus GmbH, Im Täle 2, 75031 Eppingen, Germany
Dr. Asmorom Kibrom, Nivus GmbH, Im Täle 2, 75031 Eppingen, Germany
Sources:
Abgottspon, A., Felix, D., Boes, R, Staubli, T. (2016): Schwebstoffe, hydo-abrasiver Verschleiß und Wirkungsgradänderungen an Peltonturbinen - Ein Forschungsprojekt am KW Fieschertal. Wasser Energie Luft, 108. Jahrgang, Heft 1: 9–24.
Abgottspon, A., Felix, D., Staubli, T., Boes, R. (2022): Betriebs- und Unterhaltungsoptimierung von beschichteten Peltonturbinen mit hydro-abrasivem Verschleiß – Erkenntnisse aus einem Forschungsprojekt am KW Fieschertal. Wasser Energie Luft, 114. Jahrgang, Heft 2: 105-117.
Felix, D. (2017): Experimental investigation on suspended sediment, hydro-abrasive erosion and efficiency reductions of coated Pelton turbines. VAW-Mitteilungen 238 (Boes R., ed.) und Dissertation 24145, ETH Zürich.
The Vallember weir infrastructure is part of a multi-stage system comprehensively renovated last year by the operators Engadiner Kraftwerke AG (EKW). Built in the municipality of S-chanf and originally commissioned in 1970, to guarantee ecological continuity the weir infrastructure was enhanced to include a fish ladder and equipped with an almost completely self-cleaning „Grizzly Power Optimus“ Coanda system made by the South Tyrol-based company, Wild Metal GmbH. At a length of approximately 23m, the rake surface is made up of 20 elements, forming the broadest single Coanda screen installed in Switzerland to-date. The ‘record-breaking Coanda’ screen facilitates the discharge of up to 6,000l/s of works water, while also ensuring a safe descent for fish into the tailwater section below the weir.
Engadiner Kraftwerke AG (EKW) is one of the ten largest electricity producers in Switzerland with an average annual production of around 1,400GWh of green electricity. Major Swiss energy suppliers such as BKW, Alpiq, Axpo, CKW, the Canton of Grisons and several municipalities, are all shareholders in the partnership-oriented public limited company. EKW generates the majority of its electricity with the Ova Spin pumped storage power plant and its two storage power plants, Pradella and Martina, in the Engadine Valley, connected via gravity flow tunnels and high-pressure penstocks. The plants operate a total of 13 machine groups, including five residual water turbines, to produce a joint power capacity of 412MW. Furthermore, EKW holds a 14% stake in the cross-border Inn Joint Power Plant (GKI), which started operations in 2022.
The uppermost section of the three-part plant network is the Ova Spin pumped storage power plant, whose works water is sourced from the Livignio reservoir and a total of four water catchments. The Tantermozza catchment had already been restored when comprehensive renovation work was commenced in the spring of 2020 on the other three water catchment infrastructure sites: S-chanf, Varusch and Vallember. These three water catchments are loca-
ted in the municipality of S-chanf and first went online in 1970, so some parts were in urgent need of repair and replacement. The hydraulic systems controlling various regula-
ting and shut-off valves were renewed in all the water catchments, and a number of protective screens, associated screen-cleaning machinery and items of structural infrastructure were repaired, replaced or renovated. The electrotechnical control and regulation equipment at each plant was modernised, too. “Renovation of the three water intakes had been planned for several years, but had been postponed, among other things, due to lack of personnel. Once final official approval had been granted in spring 2020, the way was clear for project implementation,” explained EKW’s project manager Curdin Barblan. In order to minimise water loss and the concomitant plant power generation reduction during the construction period, work at the three sites was staggered in three phases. Plans for the Vallember catchment along the run of the eponymous river included the renewal of structural and technical infrastructure, and the implementation of a means to ensure safe passage for fish and river-dependant life.
General renovation planning for the Vallember dam was carried out by EKW’s technical office. Straub AG, an engineering firm with a proven track record in the hydropower sector and member of the Swiss Pini Group, also played an important role in the planning process. Straub AG was charged with the analysis of the current situation, and identification of deficits prior to project implementation, and also carried out a study of options to ensure the best variant was developed for implementation by the construction management team. EKW awarded the contract for the entire con-
struction portfolio to Costa AG, based in Pontresina, Engadine. Curdin Barblan explains: “Time limitations were a major challenge for the project as work had to be completed within a single construction season to minimise water loss. Necessary watercourse diversions were dependent on construction progress on the respective infrastructure. Rather than engineering one major watercourse diversion, a variant with three smaller diversions was chosen, and worked very well.”
The basic functional principle of extracting works water laterally was also retained after renovation of the water collection basin. Prior to reconstruction, the water passed through a
coarse screen and on into a desander basin. From the desander, the water flowed over a spillway edge into a stilling basin and was channelled down a tunnel to the central S-chanf catchment weir. During reconstruction the coarse screen and spillway edge were removed, and a partition wall was erected in the middle along the length of the desander basin. Works water now flows over the partition through a Coanda rake, is collected in a trough before reaching the existing stilling basin at the end of the structure and disappearing down the tunnel. The ‘Grizzly Power Optimus’ Coanda system was supplied by the South Tyrolean industry experts at Wild Metal. The patented system is an almost completely self-cleaning protective screen for water catchments, and is suitable for use in the hydropower sector, for drinking water and for fish farms. The system takes its name from the Coanda effect, and floating debris is automatically flushed from the fine screen surface without the aid of any additional components. The entry of sand into the water intake is minimised by the extremely small screen gaps. Wild Metal relies on Inodur stainless steel to produce the Grizzly series, as it offers supreme abrasion resistance qualities. The South Tyrolians at Wild Metal supplied a total of 20 Coanda elements for the Vallember catchment, each combined with another along an approximate total width of 23m, forming the broadest Coanda system in Switzerland – and also armoured the diversion stream bodywork with 15mm Hardox steel.
The Grizzly’s fine screen was designed to provide fish with a gap of 0.6mm through which they can descend into lower water beyond the
weir, explains Curdin Barblan: “The fish pass through the partition wall in the desander and, via the screen, reach the trough to guide them safely into the tailwater below. The considerable length of the desander basin required a solution that guaranteed uninterrupted partition wall overflow. This was achieved by installing four smaller and four larger control flaps along the desander to ensure a constant water level in the headwater area, and provide the fish with a sufficiently large transition area to the Coanda system.” The flaps, which were also included in Wild Metal’s scope of delivery, optimise water intake volume instantaneously, says Curdin Barblan: “If more than 6,000l/s were taken in it would exceed the volumetric flow capacity of the penstock and cause undesired water back-up. The control flaps allow excess water to be released into the stream bed if inflows are too voluminous.” A 23-pool vertical-slot pass made of concrete elements was engineered to provide a fish ladder. After entering the tailwater area, the fish swim along a steel pipe of around 15 metres in length to the first basin below the weir. During the autumn and winter, the fish ladder is doped with a residual water discharge of 200l/s. In the spring and summer, the prescribed residual water discharge is 400l/s. Additional residual water is released through a separate pipeline into the lowest section of the fish ladder. This prevents excessive flow velocity in the tailwater, which can prove an obstacle for fish species less able to swim against strong currents.
As well as the installation of a fish passage and a Coanda system, the project also involved renovation of existing hydraulic steelwork components – such as the weir segment,
flushing gate, inlet flap and bottom outlet gate. Renewal work was carried out here by the Swiss company Fäh Maschinen & Anlagenbau AG. Project implementation commenced in mid-March last year, and the renovated water intake and fish ladder were already operating in November. “Construction work involved multiple challenges, and we knew from the test drillings we were dealing with a frost depth of about 2.30m, which of course made the job all the more difficult. It took two weeks longer than estimated to install the sheet piling, with strict safety measures required during excavation. Furthermore, the original plans for the existing infrastructure were not of requisite quality. There were no design details of the lower section of the desander. Since the
base element had been embedded in solid concrete, the dismantling work required to facilitate the installation of the new partition wall was extremely tough and time-consuming. A concrete block of more than 27m in length had to be extracted using rope cutting techniques. Ultimately, a challenging and fascinating project was brought to a successful conclusion,” Barblan affirmed. At present various tasks are being completed at the catchment site, including regreening and the installation of safety fencing. Monitoring the success of the fish ladder is to commence in May, and continue throughout the summer months. EKW is confident monitoring will produce positive findings. Initial operational observations have already shown that the fish ladder has been accepted by the river inhabitants.
• Hydraulic steelwork
• Patented Coanda-system GRIZZLY
• Trash rack cleaning machines
• Different type of gates
• Safety valves
• Different fine and course screens
• Entire water intake system made of steel
In nature, evolutionary changes usually take place incrementally, although their effects can be enormous. While developing the new ‘EVO’ turbine series, the Upper Austrian hydropower all-rounders at Global Hydro Energy GmbH subjected their Pelton, Francis, and Kaplan turbines to a complete rethink, adapting and optimising them to meet the very latest requirements in terms of environmental protection, economic efficiency and ease of maintenance. The new Kaplan EVO is the centrepiece of the promising modular shaft power plant – a further development of the patent power plant concept created by the Technical University of Munich. It’s an independent Kaplan turbine system that opens up new perspectives for previously unexploited low-head sites. The Kaplan EVO is predestined for use in both refurbishment projects, and all existing transversely-built low-head structures.
Exploitation of hydropower in the 21st century comes with a whole new set of requirements. Usage of the very oldest form of renewable energy in the modern age necessitates the questioning, and possible revision of, some of the initial premises of the first hydropower boom. The days of mega-power mechanical engineering are definitely over. Today, infrastructural considerations revolve around questions of economic efficiency, environmental friendliness, tradability and controllability. On that note, high performance is a prerequisite for less established manufacturers, too. However, there is only acceptance for technologies that meet today’s wide-ranging water ecology and environmental protection requirements, and
can be generally presented as designed to be economically viable and user-friendly. It’s no surprise the renowned hydropower company Global Hydro Energy GmbH has picked up the gauntlet of completely rethinking the machinery in the three most important types of turbines. These Upper Austrian hydropower specialists have created a brand-new line – the EVO series, putting their Pelton, Kaplan, and Francis turbines through technical developments that amount to a genuine evolutionary breakthrough. While the Pelton EVO (see report in zek HYDRO Oct. 2022) was primarily optimised in terms of compactness, simplicity and ease of maintenance, and improvement of the Francis EVO focused on an expansion of the characteristic datapoint
fields, the Kaplan EVO was specifically enhanced in the fields of environmental friendliness and ease of maintenance, achieving a previously unheard-of standard of economy in terms of low-head range efficiency.
“The roots of the development of Kaplan EVO are to be found in the shaft power plant.” The trend-setting concept of a small and completely submerged power plant was developed by the Technical University of Munich. In short, the most obvious advantages of this power plant set-up are that it is extremely fish-friendly, easily passes on bedloads and debris transported by the river, and is minimally invasive as regards its effects
upon the landscape, since the vast majority of the hydropower infrastructure is located under water. “However, in the course realising the first of the shaft power plant projects it became apparent that the costs and risks were still considerable due to individual planning and implementation requirements, and the manufacturing of the structure, and of the technical components. Consequently, economical implementation, particularly on a global scale, can only be achieved to a limited extent. Since there is further need for optimisation, the objective became the on-going development of the shaft power plant towards a modular-build system using standardised and prefabricated technical components, as well as a construction method simplified to the greatest degree possible. This was necessary to reduce the costs and risks, and to shorten manufacturing, assembly and installation times, thus creating a sustainable solution for worldwide use. As the development process continues, while we are focusing on simplifying structural implementation and optimising our hydraulics. Muhr is tailoring the steel hydraulic engineering components, and Global Hydro is adapting the new Kaplan EVO series to suit this modular system”, explains Dipl.-Ing. Bertalan Alapfy, Hydro4U project coordinator at the Technical University of Munich. “We developed the turbine-generator unit and adapted it very specifically to the requirements of the optimised system”, explains Thomas Sageder, Area Sales Manager at Global Hydro. The order was awarded to the Upper Austrian hydropower company in June 2021 as part of
the Hydro4U project – funded by the European Union as part of the Horizon 2020 research framework programme. Hydro4U aims to demonstrate the capacities of European technologies for small hydropower plants in Central Asia, and to provide planning assistance facilitating the implementation and spread of environmentally, economically and socio-politically sustainable hydropower solutions. On a detailed level, the consortium, consisting of 13 partners from 8 countries, is to work with local partners and stakeholders to install and validate two demonstration hydropower plants in Central Asia, one in Uzbekistan and one in Kyrgyzstan. Hydro4U will
provide innovative, modular and standardised hydropower solutions for low- and mediumhead applications. In addition to enabling direct market access for the participating project partners, Hydro4U is also tasked with facilitating market access for European hydropower manufacturers and service providers in Central Asia as a whole. More on the project at: hydro4u.eu.
Implementation of a modular shaft power plant is now planned for the demonstration plant in Kyrgyzstan. The power plant set-up was developed and patented by the TU
Munich, and is essentially the basis for a new type of power plant system. A vertical shaft is installed in the riverbed to link up with an existing dam or new weir, and covered by a horizontal rake with integrated rake cleaning technology. The works water flows vertically down the shaft where it flows into and drives the turbine-generator unit. No noise is generated as the electromechanical equipment is fully submerged. The weir remains under water on a permanent basis. A suction pipe through the weir body establishes a connection to the tailwater section. All technical infrastructure has been trimmed to optimise maintenance. Fish descend directly into the cushion of calmer water via special openings in the gate, the sizes of which are adjusted by means of electric drives. Extremely narrow rake-bar spacing on the fine rake screen is an effective means of preventing fish from entering the turbine shaft. Being arranged along the river, there is no need for drainage diversion, and the considerable construction work and negative environmental impacts this entails. (For more information – go to the TU Munich website). Its undisputed ecological advantages, combined with the capacity to exploit low-head sites with a maximum fall of 1.2m, open up interesting perspectives for the shaft power plant worldwide, thus also for Global Hydro – the Upper Austrian plant manufacturer responsible for the centrepiece of the power plant. “We have customised the turbine for this application, making it compact, robust and, due to the absence of oils or lubricants, extremely environmentally friendly; one that requires very littlemaintenance”, summarises Thomas Eder, Head of Production and Product Development at Global Hydro.
“Development of the double-regulated Kaplan turbine wasn’t over for Global Hydro’s engineers with the realisation of a submerged machine unit for the shaft power plant”, Thomas Eder confirms. Continued developments and functional enhancements are still being implemented. Ultimately, Global Hydro's aim was to push ahead even further with the consistent expansion of its portfolio in the low-head sector; the focus here being less on individual aspects, and more on the bigger picture overall. Thomas Sageder explains the initial situation: “How can low-pressure systems be economically viable, keeping an eye on the costs of the system overall? How can existing infrastructure be used as simply and
effectively as possible? These were questions we asked ourselves as we continued to develop the Kaplan EVO”, and added: “Machine super-efficiency does not necessarily amount to the best solution for the customer. Of course, customers at many sites can imagine installing a ‘highly-sophisticated’ bulb turbine with peak efficiencies, but what’s the benefit for operators if the infrastructure required means they will only see a return on investment after 40 years? We look at the total costs of investment. These must be reasonably proportionate to annual production. That's the key.” For those responsible at Global Hydro, it goes without saying that the new EVO-series machines don’t hold back when it comes to good efficiency. Thomas Eder expands: “We tend to be conservative when it comes to claiming machine efficiency levels. Nevertheless, the turbines in the EVO series all have peak efficiencies over 90%.”
So how does it differ to the conventional double-regulated Kaplan turbine? “The most important point is probably its submerged operation. The Kaplan EVO is designed for underwater use and all the associated consequences. We haven’t sealed the rotating components, despite it being completely submerged. The machine is water-lubricated throughout, requiring neither oils nor other lubricants, as this function is served by the ambient water,” says Thomas Eder. Water lubrication is by no means new territory for Global Hydro engineers. Thomas Sageder points out that the company has many years of experience in this field. “So far, we had only
used specially filtered water from our own water treatment unit, but in the case of the Kaplan EVO we went a step further, using ambient water cleaned of particles and suspended matter via a self-cleaning mechanical filter.” This solution also differs from the conventional Kaplan turbine in that all the actuators on the turbine are electrically and not hydraulically driven. Furthermore, the speed-controlled generator is located in the turbine housing, making it a part of the overall turbine unit.
The new Kaplan EVO was developed by the HydroLab team, as Global Hydro's development department is called, working in close cooperation with universities and research institutes. A great deal of practical experience is incorporated on top of the theoretical principles. Interdisciplinary thought is encouraged within this framework at Global Hydro. “We categorise ourselves as water-to-wire providers. As turbine manufacturers, we supply the technological centrepiece of a plant, which puts us in a position to steer decisive factors as regards the economic efficiency of a power plant – a quality also appreciated by our customers”, explains Global Hydro Managing Director Richard Frizberg, who points out that several patents have now been secured for the Kaplan EVO.
One key goal of the development work was to improve ease of maintenance; a goal achieved instyle, as Thomas Sageder affirms: “If maintenance or service work is required, the entire mechanical unit can be extracted from the water via a rail system. It can be raised with a single lift, and serviced from a walk-on platform. I've never seen this degree of simplicity with any other type of system.”
Another goal for the HydroLab team's engineers was to enhance the installability of the machine unit. “The unit is pre-assembled, tested and delivered to the construction site in one piece, so it can be installed within a few days. Mechanical installation time is estimated at around two weeks, with an extra week required for the commissioning process. Of course, being able to install a machine quickly makes a significant contribution to the economic efficiency of a power plant project”, adds Thomas Eder.
In terms of controllability, the new Kaplan EVO is fully compatible with Global Hydro's most highly-advanced control systems, such as Heros 4.0 and Heros Connect. The entire system can be monitored and controlled via the worldwide SCADA system, so customers don’t have to fear restrictions to functionality.
In addition to use in the shaft power plant, the new Kaplan EVO is ideally suited to various low-head applications – on existing transverse structures, in the field of refurbishment, at small inactive power plants, and in channels or at mill sites. “The huge advantage is that relatively little construction work is required”, states Thomas Sageder. The range of five different impeller sizes, from 800mm to 1,600mm, can serve head levels from 1.50m to 12.00m and various flow rates. “Nevertheless,” Thomas Eder explains, “we check the impeller geometry in advance for every project, and adapt it as required. The key question is whether to install a 3-, 4- or 5-blade impeller.”
An additional quality lies in the potential modularity of the Kaplan EVO, as both operational and commercial advantages can most certainly be gleaned by arranging two modular Kaplan EVOs, optimised to the discharge curves of the watercourse.
“In our opinion, the Kaplan EVO can be clearly regarded as an expansion of the low-head sector portfolio. It provides the basis for low-pressure applications to become economically viable again. It’s not about the cheapest solution; it’s about finding the one that makes the most economic sense for the customer” argues Richard Frizberg. As a result, the prospects are very promising for the Kaplan EVO. The technical principle behind the machine has been market-ready for some time. The first prototype for the shaft power plant is currently being manufactured in Kyrgyzstan and installation will be complete by the end of 2023. In the meantime, Global Hydro has already received initial enquiries for sites with natural gradients along lower-volume bodies of water; places where electricity can be generated with very simple constructions that don’t interfere with the environment to any great extent. Thomas Eder explains: “We have already received the concrete project enquiries, especially from Scandinavia, and with the Kaplan EVO we believe we are hitting the right notes.
KAPLAN - EVO
evolutionary step with multiple benefits
• Turbine unit compactness
• Lower construction costs
• Fully submersible machine unit
• Environmentally friendly: water lubrication – no oil lubrication
• Easy to maintain – excellent accessibility
• Quick construction site assembly and installation
• Viable at low-heads (1.50m – 12.00m) locations
The existing hydropower plants along the Ariége River in southern France are currently undergoing a thorough overhaul, both in terms of ecological impact and performance. The ageing power plants are being successively upgraded with modern fish passes, fish ladder systems, more efficient turbines and the latest electronics. While work was being carried out on the Grépiac power plant, it was adapted in line with the latest research recommendations on river continuity, and equipped with two new high-powered DIVE turbines, each rated at 560kW.
The Grépiac power plant is located on the Ariége River, about 45 minutes south of Toulouse by car. The Kaplan turbine plant had been connected to the grid since 1960, and retrofitted with an additional Francis turbine in 1980 in the course modernisation work. In 2016, once it had begun to fail to reach nominal output, the operators decided on complete refurbishment of the power plant. The existing turbine chambers were dismantled or closed off, and two new turbine chambers were installed on the riverbank. Enhancements to the power plant’s ecological impact included the construction
of a fish pass, the installation of a fine screen in front of the turbine chambers, and the reactivation of an existing kayak lock on the opposite bank.
In the course of modernisation, the existing turbine chambers were dismantled and replaced with new chambers with a separate mobile powerhouse. The DIVE turbines are flood-resistant and directly connected to a generator, so no machine room was required at the turbine installation site. The power electronics and plant control sys-
tem were installed in a flood-proof transport container. There are four weir panels at the inlet of the power plant, directly behind which is a very shallow vertical rake with four descent openings to the bypass leading into the tailwater. The turbine chambers are located on the weir axis and are equipped with two 560-kW DIVE turbines. The underground section of the Kaplan turbine chamber was retained in addition to two DIVE turbine chambers where, if there is sufficient water, another turbine can be installed.
Technical data:
• Head range: 2.70 - 4.00m
• Maximum volumetric flow rate: 2 x 22m3/s
• Installed power: 2 x 560kW
• Impeller diameter: 2,420mm
• Rev speed: 30rpm - 150rpm
• Total weight: 25.80 metric tons • Manufacturer:
The new fish ladder at the Grépiac power plant is a 17-chamber slotted pass. To increase the likelihood of being used by eels, cylinders were inserted in the chambers to ease their ascent and provide hiding places. Extra water is directed through to guarantee a flow rate of 1m³/s.
A shallow fine screen is inclined at 26° with 20mm bar spaces, and has a total width of 22m. The weir provides four descent openings, each at a width of two metres. Fish willing to descend without jumping the weir or following the fish ladder can reach the tailwater directly via a bypass through. The bypass is pressurised with a water flow of 2.80 m³/s and there are three cleaning rakes arranged side-by-side.
The Grépiac project faced a particular turbine technology challenge as the head is subject to stark drop fluctuations, from 2.70m to 4.00m, hence the decision to install two DIVE turbines. The chosen DIVE turbines were of a type that has become well established in the French low-head sector in recent years. In contrast to Kaplan turbines, DIVE turbines have fixed runner blades and use converters to control rotation speed, enabling efficiency to be optimised when encountering fluctuating flow rates and strongly varying heads. Although converter losses are extremely low, the Grépiac power plant uses a singly-regulated fixed-speed machine and a double-regulated variable-speed machine in combination, facilitating optimum power plant output at every place of operation.
DIVE turbines offer another benefit with regard to the increasingly extreme weather conditions. The generator is connected directly to
the turbine shaft, which has been made permanently and physically absolutely flood resistant via a patented sealing system. The water that constantly passes through the generators at the Grépiac power plant enables them to be cooled by the works water.
Although the power plant architecture makes the passage of fish through the turbine chamber very unlikely, the DIVE turbines installed here meet all the specifications for fish-friendly turbines: Fixed blades ensure there are no gaps between the hub and blades for fish to get caught in when swimming through. The blades do not require adjustment, so the gap to the impeller casing is smaller than 2mm, meaning no tolerance has to be factored in for issues such as the freedom of movement for bearings.
The nominal maximum speed of 150rpm is significantly lower than that of similarlydimensioned Kaplan turbines, and drops even further at partial loads, in turn almost completely eliminating the risk of collision for fish swimming through. The recommendation for Kaplan turbines to only operate them with completely open blades when working at full capacity is an issue for the safety of the fish population. However, DIVE turbines can offer the advantage of fully-open blades over the entire operating-load range, reducing collision risk at partial loads and lower speeds.
The DIVE turbines were manufactured at the DIVE Turbinen GmbH & Co KG production plant in Amorbach, Germany, where they were fully assembled and shipped to the south of France by HGV in harmony with planned installation schedule. This machine group can be installed on site en bloc and with very low requirements for a site’s structural tolerances,
since the generator is directly connected to the turbine shaft and the entire unit encapsulated. The benefit of this is that final assembly and extensive testing of complete machines can be conducted at the factory. The turbines were installed and wired up at the Grépiac site in a matter of hours, before being commissioned successfully in December 2021.
Subsequent to commissioning, the Ariége region experienced one of the largest flood events in 60 years caused by significant rainfall in the Pyrenees. Within 48 hours, the flow rate had increased to 1,155m³/s. The two DIVE turbines at the Grépiac power managed this impressively and showed their capacity to deal with flood water volumes. Indeed, Grépiac was the first hydropower plant along this section of the river to go back into operation after the flood.
The Grépiac power plant is now fit for future climatic extremes such as immense water discharge fluctuations.
Bilfinger Industrial Services GmbH is one of Austria’s largest domestic industrial service providers with headquarters in Linz, and subsidiaries in nine other locations in Austria and neighbouring countries. The company’s portfolio covers the entire value chain – from consultancy, engineering, manufacturing, assembly, maintenance, plant expansions and general overhauls, to environmental technologies and digital applications. Over several decades, Bilfinger has earned itself an excellent reputation as a reliable partner in the hydropower sector, having worked on a great many projects at home and abroad. Recently, the company’s specialists demonstrated their expertise handling largeformat closure elements at three large hydropower plants in Switzerland and Austria.
Lago di Vogorno is a reservoir in the Swiss canton of Ticino, serving the Gordola cavern power plant with a total storage capacity of around 105 million cubic metres. The reservoir was formed behind a 220m arch dam, constructed between 1961 and 1965, and is the fourth highest valley dam in Switzerland. Electricity is generated by releasing up to 50m³/s of discharge water from a gross head of 277m into three vertical-axis Francis turbines and one horizontal-axis Pelton turbine, to generate a total power output of just under 110 MW. In a regular year, the Gordola power plant will generate around 230 GWh of green electricity. Last year, 56 years after it was originally completed, the time had finally come to renew the hydraulic steelwork at the base of the reservoir during a planned overhaul. For this purpose, the lake was drained completely for the very first time.
Bilfinger Industrial Services GmbH received an order from Verzasca SA, the power plant operators, to dismantle two butterfly valves housed in a valve chamber. At the same time Bilfinger was commissioned by the manufacturer of the new butterfly valves, Adams Schweiz AG, to carry out the task of installation. Michael Falkner, Bilfinger’s project manager, says the project involved a wide variety of challenges: “To keep power plant down-time as short as possible, detailed planning was required prior to project commencement. One logistical challenge was that the heaviest components had to be transported away – and new ones back again –with a self-driving transporter via the narrow access road from the control centre to the shaft chamber. Inserting and removing components with a crane through a shaft 60m high and with a diameter of 3.6m required precision down to the millimetre. A bespoke fitting ring was installed to compensate axial offset when aligning the new flaps to the existing upstream and downstream connection flanges in the penstock.”
Dismantling and removal of the old components and surrounding technical infrastructure was completed in January last year. The new shut-off devices, including their drive systems, weigh 66 metric tons each, and were installed between mid-March and mid-May. Before the old valves could be removed, a special device had to be installed to enable them to be rotated 60° to be lifted out of the shaft. The new shut-off devices with a nominal diameter of DN2800 were lifted onto new foundation mountings in the chamber. In addition to installation of the new DN2800 butterfly valves, which also had to be rotated by 60° during the lifting procedure, Bilfinger‘s scope of delivery included the installation
of an oil-hydraulic control system, and piping for the hydraulic lines. Once installation work had been completed and all seal integrity checks had been made, the operating company refilled Lago di Vogorno, ready for the Gordola power plant to complete the commissioning process.
In 2019, Bilfinger was commissioned by Illwerke vkw, Vorarlberg’s largest energy provider, to install a new ball valve at the Obervermuntwerk I storage power plant, having already provided the armouring of the pressure shaft at the newly-built Obervermuntwerk II pumped storage power plant between 2014 and 2019. Obervermuntwerk I, completed in 1943, has a bottleneck capacity of 30MW and takes advantage of the height difference from Lake Silvretta to Lake Vermunt. At the time of commissioning, the plant‘s two 19MVA rotary generators were the largest hy-
dropower generators ever manufactured in Austria. Between June and September 2019, Bilfinger provided the replacement DN1500 ball valve required for emergency shutdown, installing it in its location within a valve chamber as the upstream shut-off element for the headrace. On top of assembling components and ancillary systems, order scope also included delivery and installation of the oil and water hydraulic control system.
ORDER COMPLETED IN JUST THREE MONTHS
Bilfinger‘s scope of delivery also encompassed the organisation and execution of all transport logistics and heavy forwarding to the construction site. “This included the ball valve, which – together with the drive – weighs approximately 107 metric tons, as well as the foundation brackets, the hydraulic unit and the pipe components for the ball valve control,“ says Michael Falkner. New foundation mountings had to be installed before the new shut-off valve could be installed. The new ball valve was then lifted in and aligned. A new hydraulic unit and control cabinet also had to be accommodated in the gate valve chamber. Bilfinger manufactured the oil-hydraulic piping, produced the filling and draining lines, and completed the job by pickling the weld seams on the stainless-steel pipelines. In September 2019, after all overhaul measures had been concluded, the long-serving Montafon power plant resumed regular service.
Step-by-step commissioning commenced at the Swiss Nant de Drance pumped storage power plant in 2021. Since its completion, the plant has been one of the most powerful pumped storage power plants in Europe with
a bottleneck capacity of 900MW. An altitude difference of 425m between the VieuxEmosson reservoir head and that of the lower Emosson reservoir is used to generate electricity. Primarily, the plant was designed to compensate for the fluctuating power output and irregular electricity generation of wind power and photovoltaic plants. The electromechanical equipment is located in an underground cavern. At the heart of the cavern there are six reversible Francis pump
turbines. Bilfinger Industrial Services GmbH was contracted by GE Renewable, the manufacturer, to install the each six inlet and outlet ball valves required to shut off the six pump turbines. In a regular year, the new pumped storage power plant is expected to provide about 2.5 TWh of green electricity.
Falkner recounted that the project had posed several challenges, especially from a logistical
point of view: “Several ball valves had to be installed at the same time. Since the infrastructure was all new, a whole range of suppliers and companies were required to work on the construction site side-by-side. Punctual project completion necessitated precise coordination of the available personnel.” The inlet ball valves each weigh 98 metric tons – even without drives, and were designed with a nominal width of DN2100. Even before the actuators are installed, the outlet ball valves weigh 127 metric tons, and are manufactured with a nominal width of DN2800. The inlet ball valves were designed for a nominal pressure of 65 bar, the outlet ball valves have a pressure rating of 35 bar. As well as installing the large-format shut-off devices, Bilfinger was also responsible for producing the requisite piping for bypasses and drainage lines, and for the installation of the waterhydraulic controls. Work on the order commenced in August 2017, and was completed in September 2019. Bilfinger is justifiably proud that manufacturers and plant operators around the world have relied on the Austrian company’s practical and technical expertise for the implementation of demanding projects for decades. Bundling resources and know-how creates the conditions necessary to provide customers with a complete portfolio of expertise from a single source.
No-one purchasing a generator manufactured by Hitzinger, an Austrian industrial engineering company founded over 75 years ago, ever receives an ‘off the peg’ solution. On the contrary, Hitzinger’s engineers design and finetune each machine to the needs of the customer, selecting solutions from a full range of options, tailoring to site and grid conditions, and accommodating all kinds of special requests. It’s a service that pays off. Thousands of successful plant-development projects completed around the world over several decades serve as reference works underlining the outstanding reputation Hitzinger’s generators enjoy. Regardless of how varied site requirements may be, Hitzinger guarantees the best machine for each respective application.
Last summer, in the Swiss town of Beckenried in the canton of Nidwalden, the municipality’s utilities operators celebrated completion of their latest smallscale power plant: ‘Napf’. The project became necessary due to an accident that occurred in 2013, when a slopemounted pipe to the Napf equalising basin was damaged by a landslide. The opportunity to replace the defective gravity channel with a penstock was seized, and the previously unused 70metre head was finally exploited for power generation. Moreover, the project envisioned the integration of a second water conduit leading into the power plant to enable the two turbines in the central station to be fed from two different mountain streams. An unusual
solution in terms of electromechanical equipment was chosen to achieve this goal. It involved two horizontalaxis Pelton turbines, each with its own independent supply of water, driving a single centrallylocated synchronous generator via a rigid shaft. The generator is now driven from both sides at 500 rpm. It was designed by the premiumquality Austrian manufacturer Hitzinger, adapted and optimised to suite the very special circumstances. The Linzbased mechanical engineers faced the challenge posed by the fact that each of the generator shaft ends was mounted directly to its own impeller. Resultantly, all operational safety and efficiency calculations had to be carried out for singleturbine and twoturbine operations, at full
and at partial loads. All shaft load cases were analysed via FEM using ‘Ansys’ technical simulation software. The natural bend frequency of the rotor was examined closely, too. Hitzinger used highgrade chromemolybdenum alloyed steel for the shaft, and produced greased bearings that guarantee a minimum service life of 150,000 hours. The machine group uses an aircooled generator with an output rated at 425 kVA to supply around 1.2 GWh of green electricity per year.
Hitzinger supplied considerably larger generators for two Tyrolean power plants that went into operation just a few months ago, Langer Grund and KelchsauZwiesel. Al
though both power plants are located in the same valley, the essential difference was that the Langer Grund power plant was built completely from scratch, whereas the KelchsauZwiesel power plant was existing infrastructure in need of an overhaul. In the latter case, the two original Pelton turbines, each with an absorption capacity of 700l/s, were replaced by two 4jet Pelton turbines, each with a nominal flow of 1.4m³/s. The two Pelton turbines were connected to the KelchsauZwiesel power plant. A 3MVA Hitzinger synchronous generator was coupled with each of the two Pelton turbines, and is among the larger generators in the Upper Austrian manufacturer’s portfolio today – one than now extends to machines with an impressive output of 7.2MVA. The 20metricton machines at the KelchsauZwiesel power plant can achieve overspeed of up to 1080 rpm. The new power plant is now expected to produce around 23 GWh per year, compared to the
16 GWh yielded by the old plant. That’s an increase of more than 50%. A verticalaxis 6jet Pelton turbine forms the heart of the new Langer Grund power plant, and has been designed to discharge 2.5m³/s from a 126m gross head. The 2.5MW turbine is directly coupled with a Hitzinger watercooled synchronous generator, designed for a nominal output of 3,100 kVA. Since commissioning, the machine group has performed excellently.
These standards have also been achieved at a new reference plant in the Scottish Highlands. Deanston is a traditional whisky distillery, located about 80 km northwest of Edinburgh, and has its own hydroelectric power plant. The Upper Austrian company GUGLER Water Turbines GmbH supplied a Kaplan Z turbine to replace two Francis turbines that had reached the end of their working lives. The turbine was adapted to the cubic shape of the machine building with a modern Hitzinger synchronous generator (output rating 390 kVA) mounted directly onto the turbine housing. The Upper Austrians’ proven machine constellation ensures absolutely smooth and reliable operation, as was impressively demonstrated during the first months of operation in the Scottish Highlands. The Linzbased generator specialists can invest the benefits of 75 years of experience, supplying machines designed to operate relatively conservatively, in that they offer considerable reserves and seldom operate at upper performance limits, thus are not at risk from heat buildup. This point is a key to ensuring generators have a long technical service life. Performance efficiency specifications are also stated conservatively. In all the years of its existence, the Linzbased manufacturer is
proud to have complied with almost every efficiency specification ever stipulated. Today, Hitzinger generators guarantee features ‘as standard’ that other manufacturers only make available as extras.
In the Swiss municipality of Blatten in Valais, a powerful synchronous generator was also customised for the Gisentella power plant that started operation last year. The project involved extending the existing plant that uses a head of just under 300m, and a maximum flow volume of 800l/s. The new powerhouse is equipped with a 4jet synchronous generator. A 4jet, 2.1MW verticalaxis Troyerbuilt Pelton turbine was installed for this purpose, and directly coupled to a Hitzinger synchronous generator – rotating at 1,000 rpm and designed for an output of 2.5MVA. A wateroperated cooling circuit around the generator jacket is connected to the heat exchanger in the underwater area of the machine, guaranteeing optimum operating temperatures and ensuring ultralownoise emissions when running. The new machine group has been in daily use since May last year.
A steep rise in performance was achieved by modernising the Weissenbach power plant, a powergeneration facility that had served a company of Tyrolean cement experts for almost 60 years. A few months ago, the old machine set was removed, and replaced by a solution consisting of a modern Francis spiral turbine and a directlycoupled Hitzinger generator – more specifically, a brushless synchronous generator with roller bearings, designed for a nominal apparent power output of 580 kVA at nominal speed. The
operators were very positive after the first regular months of operation. The generator alone achieved an efficiency increase of over 10%. On average now the successfully renovated power plant delivers around 62% more electricity than the previous infrastructure, so it’s no surprise the operators are very pleased with the new machine set.
The performance of these machines is only one of the benefits, as the longestablished Linz manufacturer’s machines have always offered significant advantages in terms of technical service life, too. The ruleofthumb still applies: The cooler a generator remains when operating, the longer its working life will be. For this reason, Hitzinger generators are tailormade for each respective application, and generously designed in advance with regard to the magnetic cut in order to ensure sufficient reserves. Everything works on the basis of programmes developed over decades by engineers with a vast wealth of handson experience. The programmes facilitate computation on a variety of factors and items, such as stability at speed, vibrations and bearings – and help identify the optimum machine for the location in question. In order to maintain the greatest possible control over
their own product, Hitzinger still retains a large degree of proprietary control over the manufacturing process, handcrafting most of the generator in the factory in Linz. Customers choosing a Hitzinger generator can rely on solid mechanical engineering quality, and on the fact that Hitzinger attaches great import
ance to its aftersales service. Every machine that leaves the factory bears a serial number, allowing its entire configuration to be retrieved. This is invaluable information should repair work be required. At Hitzinger, customer satisfaction continues to be the company’s central guiding principle.
Maximum flexibility in design and high quality products are our top priority. We guarantee sustainable performance for renewable energy supply. Generators - designed and built for generations.
Today, Mitterfelner Schalungsbau from Bavaria has completed more than 200 hydropower projects, and is considered the ‘go-to’ manufacturer of special formwork for hydropower plant construction. The company has supplied suction pipe formwork, bend, inlet and cone formwork, and also inlet spiral chamber formwork, since 1996. The construction of timber components is sometimes very complex, and requires a great deal of experience and finely-honed craftsmanship. Mitterfelner’s formwork is environmentally friendly, and guarantees optimal flow due to minimal surface roughness. Modern connecting systems enable large formwork components to be dissembled into smaller sections for international transportation via trucks and containers.
Without doubt, the special wooden formwork components for elbows, suction pipes and intake spirals, are some of the most spectacular items that can be seen on a hydropower construction site. Shapes are clear recognisable very early on in the construction phase, thus revealing the route the water will take through the power plant. Despite their imposing appearance, these components are products of an enormous amount of expertise and experience. Shaping concrete with formwork is still one of the more demanding tasks for hydropower projects. After all, these are usually round, curved, twisted shapes with varying radii that can’t simply be produced as standard compo-
nents. On the contrary, they really are bespoke items, tailored site conditions to the greatest possible degree. Very few companies are able to meet the multifaceted requirements of special formwork construction for modern hydropower plants. However, Mitterfelner Schalungsbau from Obermünchsdorf in Bavaria is one such business, having been active and very successful in this field since 1996. Today, the company accompanies customers along the entire project chain, from planning to manufacturing, to on-site formwork assembly.
Robert Prielmeier, Managing Director at Mitterfelner Schalungsbau explains: “Planning has evolved greatly over the past decades. The old 2D planning techniques have long since been replaced by modern 3D CAD programmes. Now, in some cases, we use 3D models from the printer for a better standard of
visualisation. It is essential for us to be familiar with all common CAD programmes, as the requisite formwork design is usually predefined by each turbine builder’s construction specs. That's why today we also have graphic drafting programmes with more than 60 interfaces to all the most commonly-used CAD programmes on the market.” Regardless of the degree of planning tool sophistication, human expertise remains indispensable for implementation. Extremely complex bespoke formwork is made largely by hand. “Each component has different radii, curvatures and shapes – and this demands craftsmanship and skill,” adds Prielmeier, pointing out that building formwork is a core activity of the joinery and carpentry trades, and admitting that although, for this reason, apprentices at Mitterfelner Schalungsbau are still trained in these trades, it is becoming increasingly difficult to find young talents.
Mitterfelner Schalungsbau’s particularly high standards of expertise in the production of special formwork for hydropower plants can be explained by the fact that the founding family has operated its own hydroelectric power plant for several generations. Hydropower is, so to speak, in Mitterfelner’s DNA. In 1996, the company conducted a thorough conversion of its own hydropower plant, thereby determining the direction of the company's commercial development moving forward. Managing Director Prielmeier expands: “That’s also why the idea of environmental sustainability plays such a big role for us, and why we still rely on natural, untreated wood from locally felled timber.” This makes good sense, particularly if the issue of disposal in the construction industry is considered more closely. Prielmeier draws the comparison with tunnel construction – in which other types of formwork skins are often used. Once these have been contaminated with cement slurry, they have to be disposed of in a very timeconsuming and expensive manner, whereas disposal of Mitterfelner's wooden formwork is relatively simple. Indeed, after use the elements are often cut up for use as firewood. Robert Prielmeier explains the advantages of untreated wood in more detail: “Wood extracts water from concrete, resulting in fewer air pockets and cavities – making it harder and more resistant.” In some cases, if structural conditions permit and the customer wishes so, formwork can be used multiple times. The formwork is solidly braced in the factory, so it’s ideally suited for re-use.
Not uncommonly, on-site spatial conditions at a power plant are too awkward to allow the insertion of formwork en bloc. In such cases, it is essential to include the option of dissembling formwork into smaller sub-units. To guarantee this flexibility, Mitterfelner Schalungsbau deploys a functional and robust connection
system to enable simple and safe assembly and disassembly. Divided in this way, formwork components can be transported over long distances in trucks or containers, and be reassembled on reaching the construction site. Nowadays, every hydropower operator attaches the utmost importance to optimising flow conditions within the plant. The smoother the surface of a water channel along which the works water flows, the smaller the loss of energy via friction, and the greater the efficiency and profitability of the power plant – be it the surface of a penstock or an intake spiral. Mitterfelner pays special attention to the outer surface of the formwork, filling pores and
sanding it with fine sandpaper. Ultimately, the meticulous and precise approach to preparation pays off, not least because the majority of hydropower operators in Central Europe rely on the special formwork manufactured by Mitterfelner Schalungsbau. The successful completion of more than 200 projects bears reference to the quality of this work. Mitterfelner Schalungsbau’s expertise can be marvelled at in a whole range of hydroelectric power plants – in high-alpine pumped-storage power plants, such as the Obervermuntwerk in Vorarlberg, small and innovative shaft power plants in Bavaria, and large run-of-river power plants on the Inn and Mur rivers.
Since last summer there’s been a new 3-man leadership team on the board of the northern Italian steel construction company PELFA Group Srl. The company was founded in the town of Buja at the end of the 1970s by Redento Fabbro, who managed and developed the business successfully for four decades. Now, the reins have been handed over to Andrea Forgiarini, Daniele Fabbro and Alessandro Bertino. PELFA is a well-established steel construction company that stands for high-quality industrial components for the energy sector, railways, military, lifting technology sector and the construction industry. Hydropower projects now account for around 50% of PELFA’s order volume and the company has earned a particularly distinguished reputation in this field. The Kühtai 2 power plant in Tyrol and the Reißeck 2plus power plant in Carinthia are two of the most recent and spectacular reference projects in the company’s portfolio.
When the company’s founder Fabbro Redento handed over executive power to his successors at the PELFA Group in July last year, it marked a small but significant turning point. Redento built up, expanded and positioned the company successfully in the international steel construction market for more than 40 years. The changing of the guard was completed to ensure all this good work and
success continues. The company’s shareholding majority has been taken over by Andrea Forgiarini, Daniele Fabbro and Alessandro Bertino, who have worked closely with the company founder in management functions for several years. The three new PELFA chief executives stand for theoretical expertise, practical know-how, and for continuity. Andrea Forgiarini represents the company externally as President of the Board of Directors and is responsible for relations with customers, banks and administrative management. Daniele Fabbro runs the entire steel construction and welding production operation, and Alessandro Bertino is in charge of the mechanical processing and assembly departments. Andrea Forgiarini states: “We aim to continue pursuing the trends and developments of recent years, and to expand into new and challenging markets, while remaining as competitive as ever.”
Forgiarini has been CEO at PELFA since 2004 and points out that the company has great respect for its employees – explaining that they are the most important factor in the company’s success. An appreciative corporate culture promotes positive interaction among employees, and is a major key to guaranteeing smooth and open cooperation and communication between departments. “This ensures there is little employee turnover, and much-valued expertise remains within the company. And that’s of benefit to our customers, too” declares Forgiarini. Another secret of PELFA's success is an unceasing will to develop. The company invests heavily in state-of-the-art equipment and machinery, as well as in the specialisation of its own staff. PELFA is convinced this is the only way to stand out from the competition in the medium term. This approach also
explains the company's ability to adapt to the latest challenges within the industry. The northern Italian company has reacted to high energy tariffs and rising raw material prices by developing a number of strategies: It has implemented several measures to improve energy efficiency in production processes, installed a photovoltaic set-up and new energy-saving systems. Moreover, PELFA relies on close cooperation with trusted suppliers to ensure a sustainable supply of raw materials and all requisite components.
The PELFA Group has grown immensely, especially in the hydro sector. The hydro sector accounts for about 50% of the company's total current order volume. “The hydro sector has facilitated qualitative growth in the past, and is incentivising continuous growth moving forward”, states Andrea Forgiarini. In the industry today, PELFA has established a reputation for being able to produce large components with a high level of technical complexity – investing all its expertise and keen attention to detail. “At PELFA, we continue to strive to be flexible and quick to respond to market challenges. Similarly, we are strongly committed to maintaining high product quality and reliability”, he adds.
PELFA’s customer reference list alone speaks volumes about the qualities the company offers. Over the past months and years PELFA's client list has included giants of the industry – such as VERBUND, Voith Hydro, Braun and DSD Noell. Most recently, the company supplied the spirals for the Reißeck 2plus power plant and is currently manufacturing spirals for the Kühtai 2 power plant project in Tyrol. Suction pipes, inlet pipes, ball valves and sluice gates have already been delivered, and similar components have been supplied to hydroelectric power plants all over the world in the last few years. The history of PELFA is a success story, no more – no less; and one now being continued by the new and highly-motivated trio at the head of the company.
The future of hydropower in times of an accelerating change of the world’s climate will be strongly affected by the subsequent changes and geographical shift in precipitation (IPCC, 2013). This will have impacts on the ecology and possible uses of rivers. With the growing accuracy of models, predictions can be made for both global and regional water availability. Following modelling results, there is a consensus that extreme weather events such as heavy rainfall are on the rise (Jjunju et al., 2022). In addition to well-known consequences such as floods or landslides, there is also a little-known danger for fish and aquatic invertebrates introduced by hydropower plants: total dissolved gas (TDG) supersaturation.
With gas supersaturated liquids are primarily known to us from beverages, where typically CO2 is dissolved under pressure in the liquid. This creates for example carbonic acid in mineral water. The opening of the bottle or can leads to a pressure drop leading to gas bubbles escaping the liquid, representing a natural way of degassing. This example illustrates the principle of TDG supersaturation, which follows Henry's law: the solubility of gases in liquids is directly proportional to the pressure in the liquid. Supersaturation exists when there is too much gas dissolved in a liquid in relation to the liquid’s pressure. Temperature also has an influence on the solubility of gases, which is less relevant in this case.
The most important parameter for energy generation in hydropower plants is, next to the flow rate, the head, which determines the pressure. If air is entrained into the water that flows into the hydropower plant’s waterways and there subjected to high pressure, it dissolves in the water. This can occur in medium or highpressure power plants, for example, when air is introduced into the system due to blockages or inadequate sizing of the inlet. Often, this occurs during heavy rainfall events and other high flows such as snowmelt, but also in cases where the inlets are too shallow or underdimensioned. The turbine type is important for the formation of TDG supersaturation. In most
Pelton turbines, the water is adequately aerated when it leaves the turbine blades, while in Kaplan and Francis turbines, there is hardly any degassing due to the full submergence. In other cases, TDG supersaturation can occur at high dams on large rivers when, during flood discharge, air is introduced into deep water depths below the dam. Measurements have shown TDG saturation levels of up to 120% in connection with turbine aeration for operation at maximum capacity (Pulg et al. 2018).
TDG supersaturation can have potentially severe consequences for fish and aquatic invertebrates in the water ways downstream the hydropower plant. When fish are exposed to increased TDG saturation, a condition called gas bubble disease can occur, which shares similarities with the decompression sickness in humans. This condition is characterized by the formation of gas bubbles within the organism, often in the fins or eyes of fish, due to an increase in the concentration of
gases. The severity of the disease depends on the level of TDG supersaturation and the exposure time as well as the species of fish and its size and age. Acute cases often lead to gas embolisms within the blood vessels or vital organs, resulting in death. Less severe cases are reversible but may lead to secondary injuries such as fungal infections and stress. Gas bubble disease can occur even at low levels of TDG supersaturation and can be lethal at levels above 110% TDG saturation (with 100% saturation describing the normal state). This value is also defined as the threshold in some US states and in Canada for rivers with a water depth of more than 1 meter (Weitkamp & Katz, 1980). Studies in North America, China and Norway show that TDG supersaturation caused by hydropower is a widespread and underestimated problem. In the United States and Canada, the first investigations into
hydropowerinduced TDG supersaturation were conducted as early as the 1960s. There, as well as in China, the problem is mainly occurring at high dams. In contrast, in Norway, where Francis turbines are predominantly used for medium to high head installations, TDG supersaturation is a major issue. The international research project SUPERSAT, led by the Norwegian Research Centre (NORCE), has in recent years been investigating the prevalence of TDG supersaturation in Norway, Germany and Austria. The research within Austria has been conducted by the University of Natural Resources and Life Sciences (BOKU), while the University of KoblenzLandau was responsible for the German part of the research. Preliminary results show that a significant proportion of large Norwegian power plants have a high to very high risk of creating TDG super
saturation. Work is currently underway to develop comprehensive monitoring of the downstream water ways (Pulg et al., 2020).
The formation of gas oversaturation can be prevented by avoiding air entrainment into pressurized water. This can be ensured, for example, by using special hydraulic structures at dams or by appropriately dimensioning power plant inlets. If the formation is unavoidable, degassing by aeration can be accelerated by venting water over weirs, thresholds or through deflectors (Pulg et al., 2018). In Canada, the use of ski jump highwater release structures for degassing has been successfully tested (Kamal et al., 2020). In the Norwegian DeGas project, further technical solutions for rapid degassing of dissolved air are being developed, with a focus on the use of power ultrasound and bubble curtains (Rognerud et al., 2020). Preventing TDG supersaturation in water ways downstream hydropower plants will become more relevant due to climate change. The aforementioned increase in heavy rainfall events is expected to lead to more TDG supersaturation events, particularly in mountainous regions with reservoirtype power plants using Francis turbines and secondary inlets. Therefore, when TDG supersaturation is suspected, a measurement system should be installed to continuously monitor the TDG level at the power plant outlet. Combined with data from power plant operations, possible causes of TDG supersaturation can be identified and fish deaths can be prevented. This contributes to achieving the criteria of environmental regulations, animal, nature and species protection, as well as the Water Framework Directive and the EU Taxonomy.
[writers: Wolf Ludwig Kuhn & Dr. Ulrich
Pulg & Sebastian Franz Stranzl]
Literature
Jjunju, E., Killingtveit, Å., & Hamududu, B. (2022). Hydropower and Climate Change. In Comprehensive Renewable Energy (pp. 259–283). Elsevier. https://doi.org/10.1016/B978-0-12-819727-1.00111-4
Pulg, U., Isaksen, T. E., Velle, G., Stranzl, S., Espedal, E. O., Vollset, K. W., Bye-Ingebrigtsen, E., & Barlaup, B. T. (2018). Gassovermetning i vassdrag-en kunnskapsoppsummering (No. 312; Issue 312). Labora torium for ferskvannsøkologi og innlandsfiske.
Weitkamp, D. E., & Katz, M. (1980). A Review of Dissolved Gas Supersaturation Literature. 45.
Pulg, U., Stranzl, S., Wagner, B., Flödl, P., & Hauer, C. (2020). Gasübersättigung in Flüssen? Messung, Ursachen und Auswirkungen – Ein internationales Forschungsprojekt untersucht Verbreitung und Umwelteffekte. Österreichische Wasser- und Abfallwirtschaft, 72(3–4), Article 3–4. https://doi.org/10.1007/s00506-020-00655-y
Kamal, R., Zhu, D. Z., Crossman, J. A., & Leake, A. (2020). Case Study of Total Dissolved Gas Transfer and Degasification in a Prototype Ski-Jump Spillway. Journal of Hydraulic Engineering, 146(9), Article 9. https://doi.org/10.1061/(ASCE)HY.1943-7900.0001801
Rognerud, M. E., Solemslie, B. W., Islam, H., & Pollet, B. G. (2020). How to Avoid Total Dissolved Gas Supersaturation in Water from Hydropower Plants by Employing Ultrasound. Journal of Physics: Conference Series, 1608, 012004. https://doi.org/10.1088/17426596/1608/1/012004
Actuator manufacturer AUMA supplies electric actuation solutions to adjust the guide vanes of submersible hydro turbines. Such a solution is in operation at the Sauerbrunn hydropower plant near Graz, Austria, in combination with a fullysubmersible RHT turbine from Natel Energy.
California-based turbine manufacturer Natel Energy required an actuator that could operate continuously underwater, provide accurate positioning to optimally control the water supply to the turbine, and send feedback signals to the higher-level PLC. Previously, their only option was a hydraulic actuator. AUMA suggested an electric actuation solution that provides better control and feedback at a much lower total cost. The AUMA SARV-UW actuator for continuous underwater use proved to be ideal for this application. It provides high positioning accuracy (≤0.2 %) with continuous feedback to the higher-level PLC. The actuator is controlled by the PLC via Profibus. The ability to mount the actuator controls separately is an extra bonus that allows the end user to operate the actuator locally should the PLC fail. The low power consumption of the SARV also allows the end user to utilise an uninterruptible power supply (UPS) as a backup in case the main power is lost.
AUMA actuators for continuous underwater use possess a sophisticated sealing system combined with excellent corrosion protection. Double-sealed cable glands at the electrical connection, inner seals at all housing covers, and a solid shaft made of stainless steel ensure safety by preventing any ingress of water.
The SARV-UW is equipped with ACV 01.2 intelligent actuator controls. In addition, AUMA supplied a GS part-turn gearbox and a custom lever arm assembly rated for continuous immersion that is used to adjust the guide vanes. The local AUMA team in
California also provided training, commissioning, and testing support to Natel Energy. The AUMA solution has been successfully in operation in Sauerbrunn since autumn 2022. The small hydropower plant was integrated into the Muehlgang, an existing bypass channel to the River Mur. With the 15 kW RHT turbine supplied by Natel Energy, the operator, Energie Steiermark, aims to generate environmentally friendly electricity for the municipality of Großsulz. Natel Energy is a specialist in innovative, fish-safe, fully submersible hydro turbines.
„Especially nowadays, when the impact of fossil fuels is omnipresent and we are more and more confronted with the effects of climate change, hydropower is becoming increasingly important. Providing sustainable technologies for future generations means to focus on delivering the best quality to our customers as well as to work on the development of technology that will help us combat the climate change.“
As Head of Small Hydro in Austria, Radu Carja helps to achieve these goals and finds the best solution for our customers.
Radu Carja Managing Director Small Hydro Austria